At the beginning of the product development journey, you may see an overwhelming number of engineering approaches, recommendations, and practices, each promising you guaranteed success.
However, don’t fall for the first available option. While some recommendations might be perfect for one business, they might be a total mismatch for you. Thus, it is pivotal to find the best-fit path for your project, considering its goals, specifics, and budget.
In this article, we cover the popular engineering approaches that will allow you to validate your product idea from an early stage to determine whether it is feasible and worth investing in and what steps you need to take further.
Keep reading to gain a clear understanding of PoC, prototype, and MVP and learn what are the core differences among them.
What is PoC?
PoC, or Proof of Concept, is a product development approach that aims to validate an idea’s feasibility before the development process begins.
As embedded products commonly have complex functionality and communication, using PoC is an optimal approach.
This approach uses off-the-shelf components like evaluation boards to check whether your product will operate as expected, oversee potential challenges, and make adjustments before the development phase.
If PoC is successful, you can move forward with the next steps, including estimating and checking if the end product will meet your deadlines, budget, and scale expectations.
Reasons to build a proof of concept
PoC is not available for user testing or any kind of external usage; it is an instrument to internally test your product and determine whether it is worth investing in.
Nevertheless, this approach helps determine the further development iterations. Mainly, when you decide to build a PoC, it brings you the following benefits:
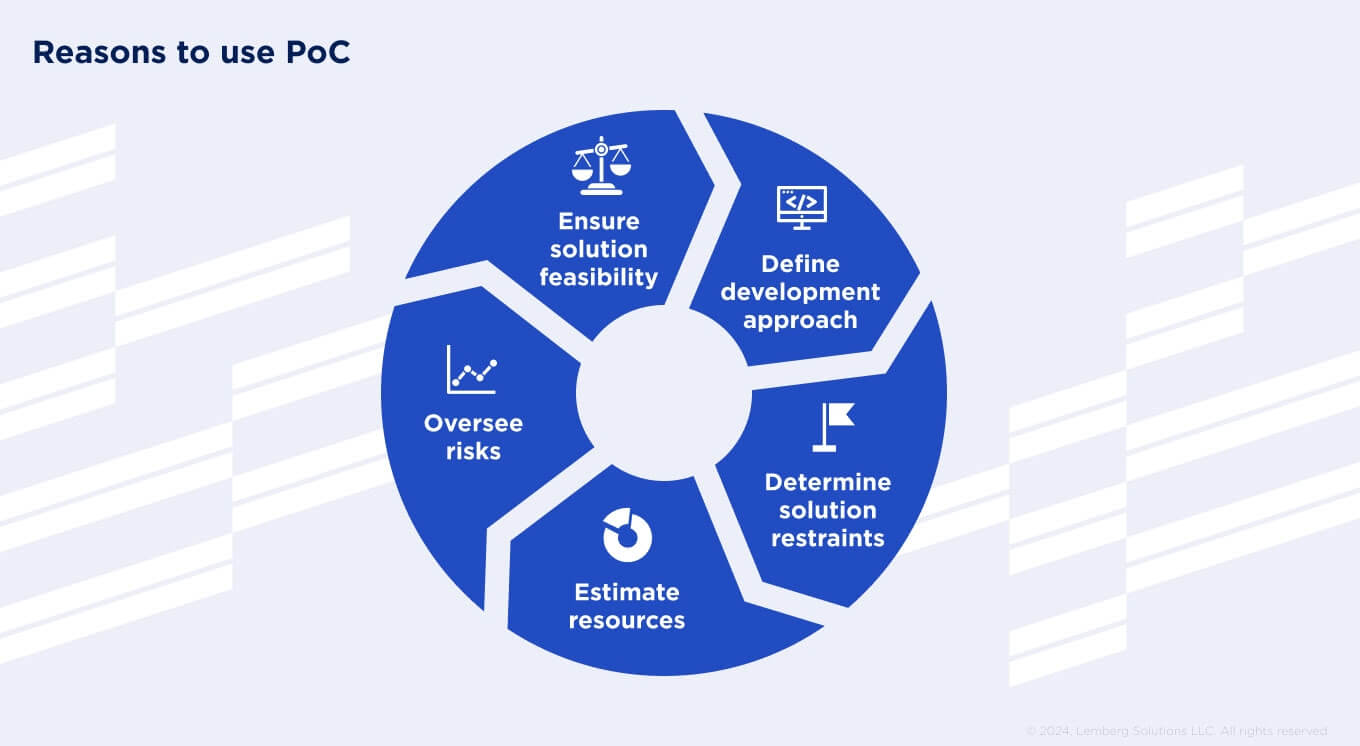
- Determine the development approach, required dev tools, and tech stacks to complete the project as expected
- Ensure your solution idea is feasible and can be technically implemented
- Define the product restraints in functionality and capabilities
- Estimate the resources you need to develop your solution
- Predict potential risks and failures that may happen in the subsequent iterations.
Best practices for creating a PoC
Before creating a PoC, it is vital to consider entry points, including your requirements and expectations from this iteration.
Get your clear goals set up
You should define your expected output product to get a better understanding of the PoC version of a product. This will ensure accurate results and the success of this stage, which aims to check the functionality of your future embedded solution.
Determine measurable success criteria
The next vital step is to set the criteria for determining whether your PoC development is successful and fully aligns with your business needs. While testing the product feature with PoC, you should clearly know what you expect: improved system performance, better user experience, or reduced resources.
Document the PoC development process
Documentation is pivotal at each development stage. Structured product documents allow you and your engineering team to understand how your solution works and what it consists of. You’ll also avoid missing details, easily switch between tech vendors, and onboard new engineers on your project effortlessly.
Moreover, your project documentation should be updated, including the challenges you've encountered and other notes vital to consider in the next engineering iterations.
Evaluate the results
As soon as the scope of your PoC is delivered, you will easily define its success due to the previously set criteria. If the solution matches your initial requirements and business goals, you can use a PoC for prototype or MVP development iterations. If not, you have enough time to make adjustments, avoiding the risks determined during the PoC while building your product.
Example of proof of concept
To showcase a PoC development example, let’s review a PoC development project we delivered for Speede, a sports tech fitness device.
Speede is a US-based startup that aims to make workouts shorter and more efficient by incorporating individual approaches using a smart device.Their product required isotonic, isokinetic, and eccentric training, which is pricey, meaning the startup needed to raise enough investment to complete the device. Thus, Speede requested PoC development to validate their concept and show its value to stakeholders.
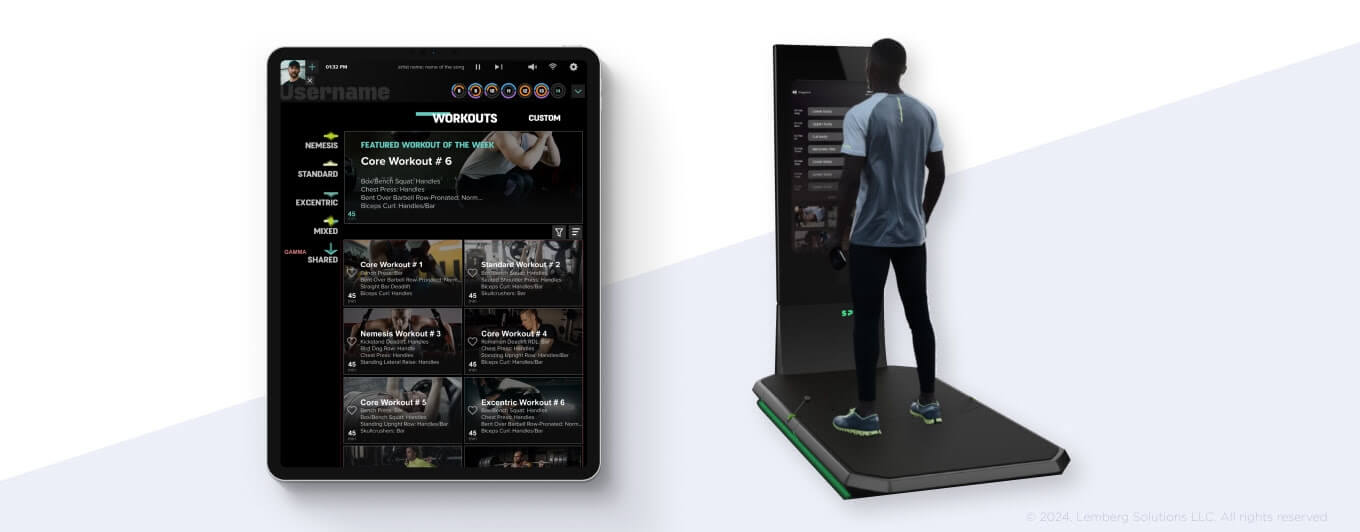
Our embedded engineering team built a high-fidelity product prototype in the short term, including a 3D model, hardware component selection and integration, and firmware. This allowed our clients to ensure the concept worked as expected and eventually helped them convince investors of its worth to proceed with the subsequent engineering iterations.
See more details on the PoC development and learn about the plans for the next stages.
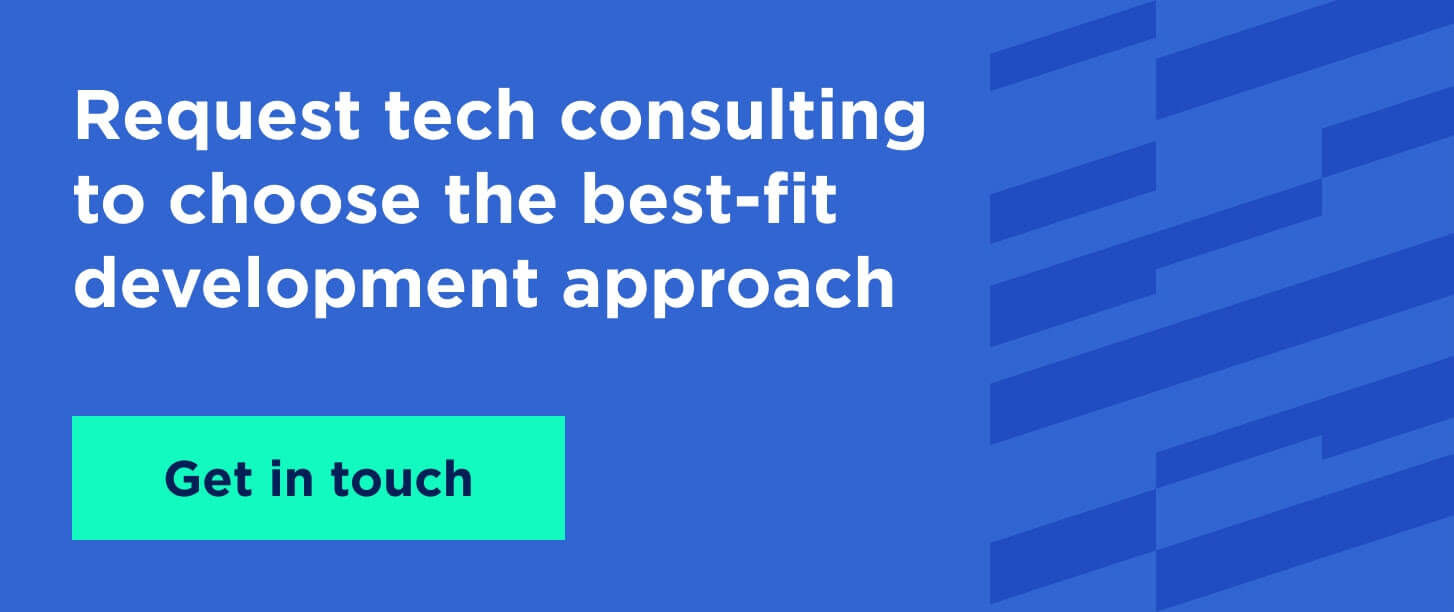
What is a prototype?
An embedded product prototype is the very first version of the product. Unlike PoC, the prototype is the very first version of a working product with all the functionalities you need. However, you will still have to collect user feedback on its usability and test some features to see how they actually work.
Types of prototypes
Depending on your initial goals and expectations for product prototyping, you can choose from the following types.
Rapid prototypes
Rapid prototyping is a relatively quick approach to creating the first version of your product and testing its basic functionality. This method helps engineers quickly create a prototype, test and validate various concepts on real users, and outline the risks and issues that may appear during the actual development phase. Rapid prototypes can speed up product development but are not reusable for subsequent iterations.
Industrial grade prototypes
This is a good choice if you already manufactured some samples and want to build something more reliable and ready for mass manufacturing. Usually, this type of prototype is as close to the end product as possible.
Mass manufacturing prototypes
This type of prototype is ready to be mass-produced and optimized accordingly. Developing such a prototype requires detailed specifications from the beginning and thorough testing. If it doesn't work as expected in terms of functionality, thousands of devices will be affected at the mass production stage.
Reasons to use product prototyping
Summing up the primary benefits and options of product prototyping, let's review the main reasons to kick-start your project with this iteration:
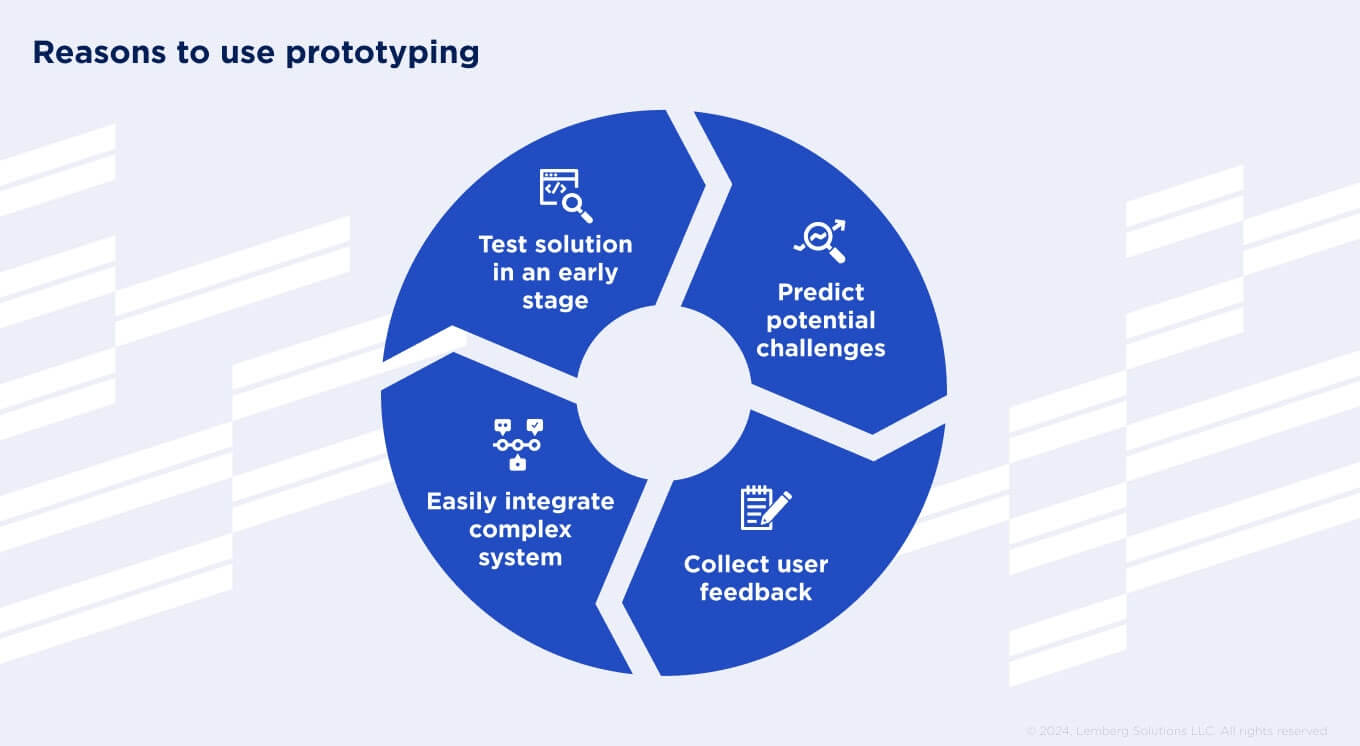
- Prototyping provides a great opportunity to test the product, measure its correspondence to your requirements, and see what changes should be made in the next iterations.
- Engineers can determine potential risks, challenges, and weaknesses during prototyping to avoid or fix them further, saving resources and costs.
- Product prototyping also entails collecting user feedback before the mass manufacturing phase to make timely adjustments.
- Opting for prototyping is also helpful for complex and scalable solutions, where an iterative engineering approach helps validate the feature set, define issues, and ensure the smooth integration of all components into a functional solution.
Example of a prototype
Let’s review the prototyping process based on an example from our experience.
Our embedded engineers received a request for rapid prototyping for a biotech moss-based air purifier. The concept of this solution was to investigate whether moss is efficient enough for quality air purification.
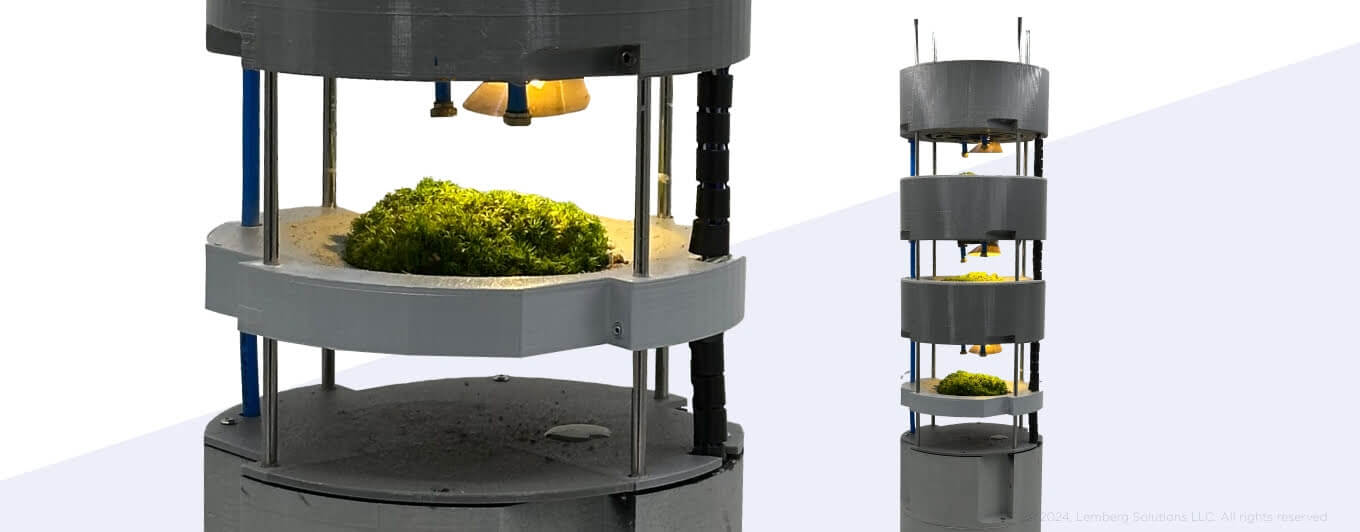
The Lemberg Solutions team built a prototype and took on mechanical and electrical design creation as well as firmware development to make the prototype functional. We also worked on selecting suitable hardware components that would match the product size and initial requirements.
See how the development process was happening.
What is an MVP?
The difference between an MVP and a prototype is that an MVP, or Minimum Viable Product, is a functional solution with a limited number of features. It is certainly not the final version of the product that can be used for its purpose. However, an MVP showcases how the final product will work, demonstrating core functionalities.
MVP is a standard tool for those who want to attract investors to product development or show the first results to investors to prove its viability. That is why MVP usually operates the most “selling” feature set.
Common types of MVP
You can choose between two primary types of MVP – low-fidelity and high-fidelity. Let's see which one best fits your project development criteria.
Low-fidelity
A low-fidelity MVP doesn't entail programming. Its primary purpose is to illustrate the future product and show its value to users or stakeholders. This type of MVP doesn't display the actual operation but ultimately reflects the concept and its potential feature set. Low-fidelity MVP provides several ways to present the information: demo video, landing page, questionnaire, etc.
High-fidelity
A high-fidelity MVP is a more complex approach that includes working on a complete feature set. It allows first users to test it, provide feedback, make changes, and proceed with the development. Although a high-fidelity MVP takes more time and effort than a low-fidelity MVP, it will save you development costs in later engineering stages.
Reasons to build an MVP
MVP goes far beyond feasibility validation. It provides a working product version and demonstrates its features in action. If you are still hesitant about MVP vs prototype as an option for your project, let's sum up the reasons to go for MVP:
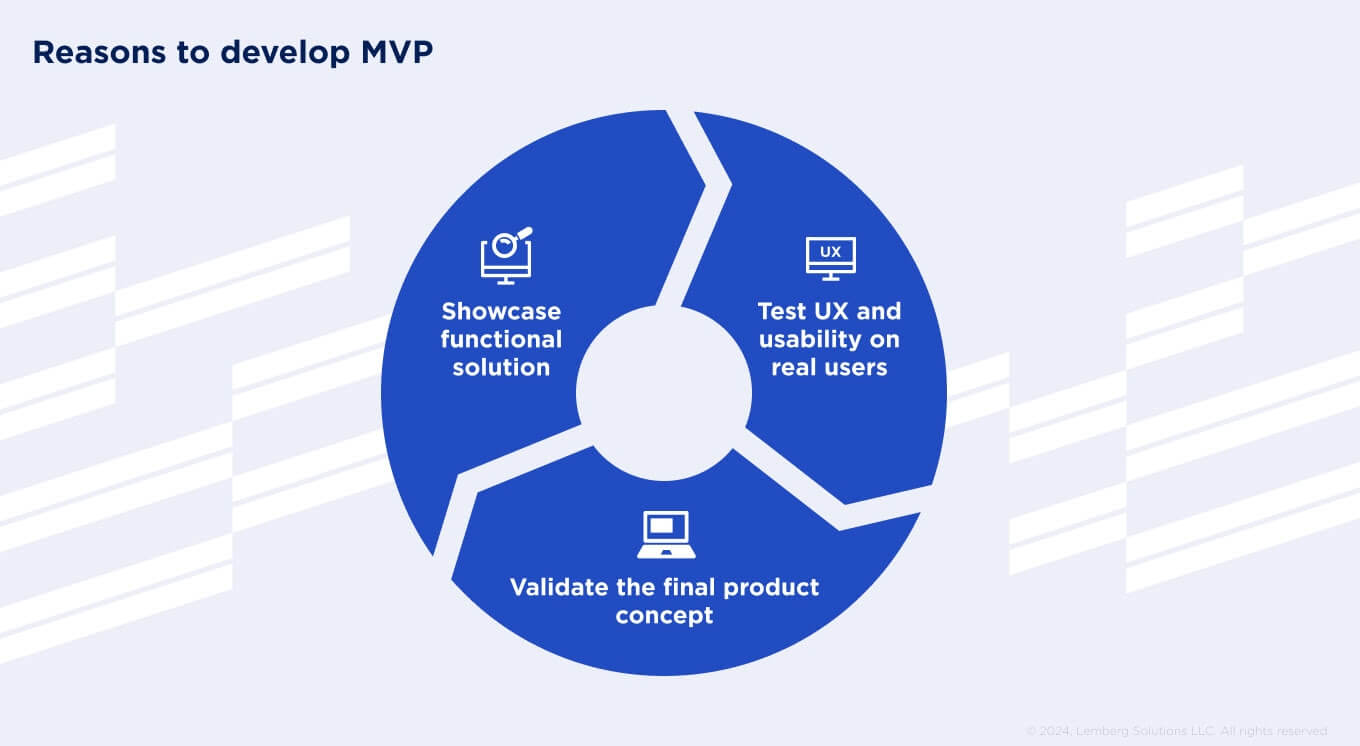
- Developing an MVP is a helpful approach to presenting your product idea to potential investors if you are an early-stage startup, ensuring you have previously validated its feasibility.
- MVP allows collecting user feedback at an early development stage to test the product's UX and usability and make timely adjustments, saving costs and resources for future iterations.
- By gradually developing your solution, you ensure the success of the final product version. MVP development gives you time and capability to validate your product concept, create excellent UX and appealing UI, oversee potential risks, and gather feedback before proceeding further.
Example of a minimum viable product
To help you better understand the value of MVP development, check out the minimum viable product we built for a healthcare device by TCC.
TCC is a German-based healthcare unit that provides digital intensive care. It uses AI technology for preventive care and disease course prediction.
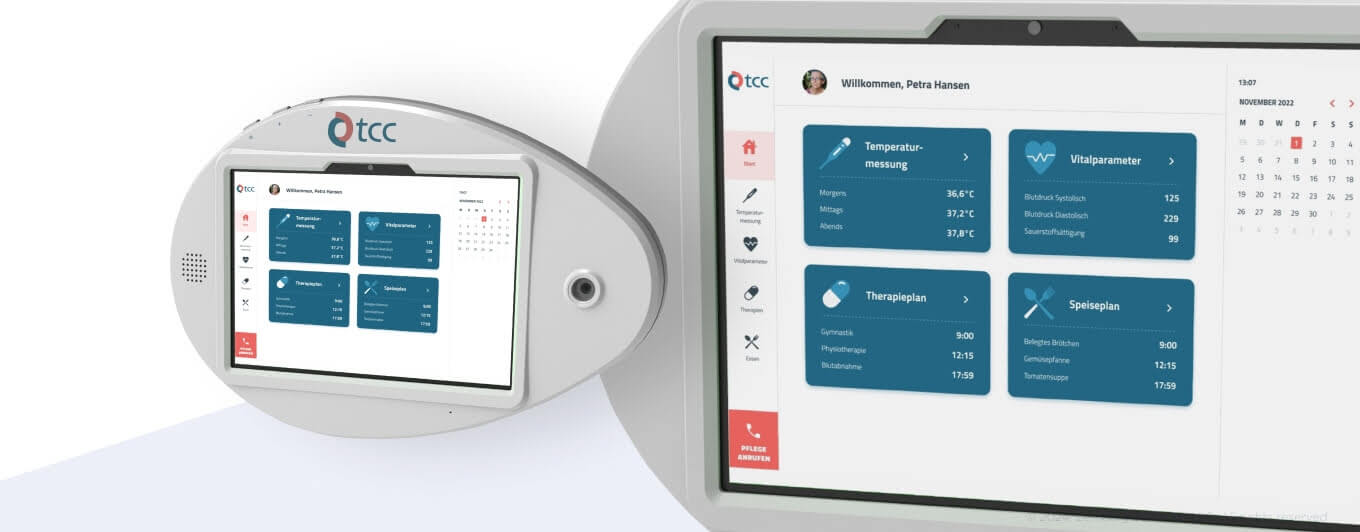
Their initial goal was to develop an MVP of an electronic nurse device to validate the concept, ensure it can be technically implemented, and convince stakeholders of its value. Our embedded engineering experts created an industrial design for the electronic nurse device MVP.
The next iteration included developing an IoT prototype and integrating it with the required services that let patients and physicians track health vitals, including temperature, heart rate, blood pressure, and oxygen level.
Read more about this medical device MVP development and learn how it works.
Key differences: PoC vs prototype vs MVP
Let's compare the core differences among PoC, prototype, and MVP to help you make a choice quicker and more effectively for your project.
Proof of Concept (PoC) | Prototype | Minimum viable product (MVP) | |
---|---|---|---|
Goal | Validate product technical feasibility | Determine how the product will be built and collect feedback from test users | Showcase how the product works and collect feedback from real users |
Risk evaluation | Determines potential technical issues | Oversees the required resources to complete the product and user expectations | Validates product market demand and readiness for mass production |
Used for | Test new product ideas and worthiness to start development | See how the product works to convince stakeholders of its value | Looking for a market niche, considering real users' feedback |
Next iteration | Prototype or MVP development | MVP or product development | Product development |
What to choose for your project: PoC vs MVP vs prototype
There is no need to compare the difference between MVP and prototype, as they have different purposes and fulfill different needs and goals. Overall, PoC, prototype, and MVP are just different engineering stages. So you can go for one as well as all of them for your project based on your business needs and specific requirements.
- PoC helps you dispel doubts and oversee potential risks for product development, determining whether the solution is worth investing time and money.
- The prototype also relates to the pre-development stage, which allows you to visualize the future solution and collect feedback before proceeding with the next iterations.
- MVP provides a functional solution with a limited feature set to future-proof the market demand and incrementally develop the product, considering user feedback.
Summing up
If you are looking for tech consultancy for your solution in the PoC, or prototype, or MVP development stages, or want to kick-start your project, you’re in the right place. All you have to do is fill out the short form and share a few words about your project so we can process your request and come back to you with the best-fit solutions.
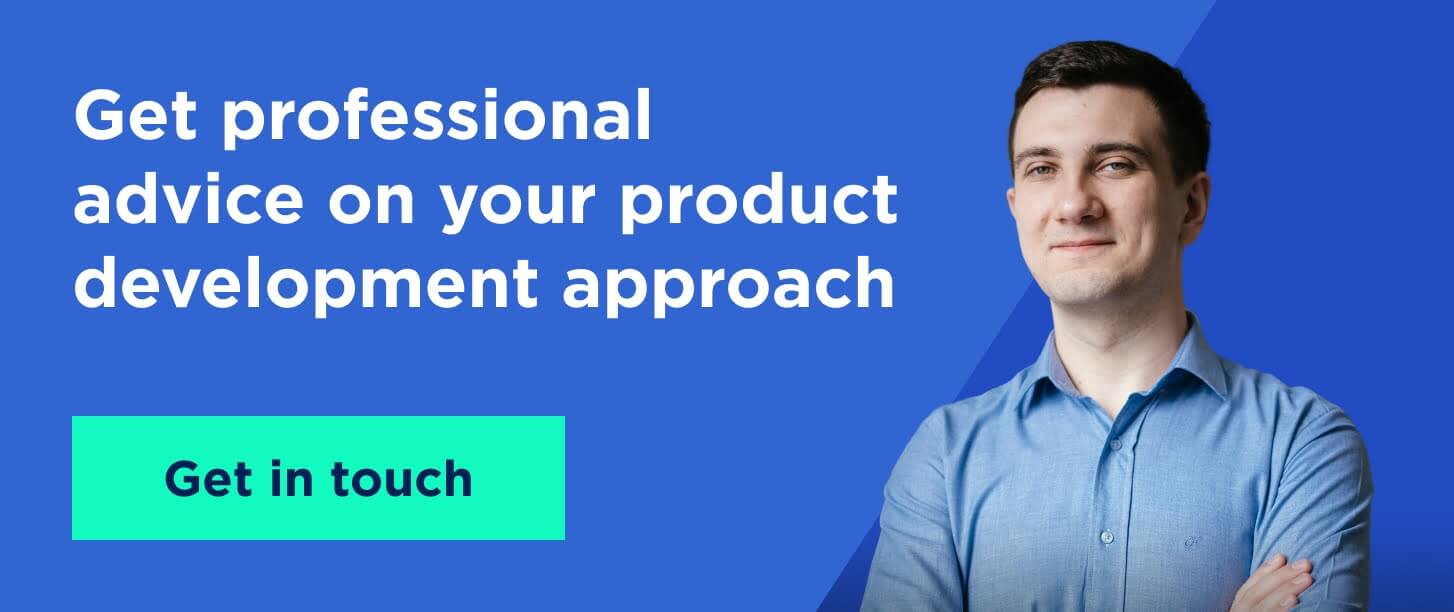