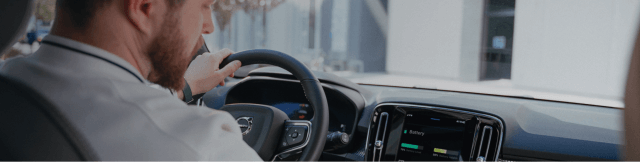
Automotive battery management system with advanced SoC and SoH algorithms
The challenge
We aimed to build an advanced battery management system with improved accuracy of SoC and SoH algorithms for hybrid electric vehicles and electric vehicles. Our demo was built using automotive grade components and designed to conform to ASIL-D certification. The scope of work covered such safety features as Over/Under Voltage, Over/Under Temperature Protection, Short Circuit Detection, Cell Balancing, CAN Communication, and Faults Handling.
Delivered value
Lemberg Solutions’ data science team developed enhanced SoC and SoH algorithms that suited the requirements of high-reliability automotive applications. These algorithms use data from such sensors as temperature, current, battery chemistry, and capacity — thus enabling 96–98% SoC algorithm accuracy. Our algorithms ensure correct driving range determination, prolong battery pack lifespan, and reduce the risk of fire incidents. Our software development team implemented this algorithm along with a human-machine interface and other functionality.
The process
The LS embedded software development team was able to quickly kickstart this project on development boards before the custom PCBs were delivered. This helped us to write the code iteratively, before deploying it to target boards.
Initially, our data science team reviewed use cases for cars, such as when sudden temperature drops occur after the car leaves a warm garage and encounters low winter temperatures, or when battery drainage happens in cars that have been parked for several days. We also considered various indexes like temperature, range of currents, chemical compounds (li-ion in our case), and capacity. This knowledge enabled us to build highly accurate SoC and SoH algorithms throughout later development stages.
We used the AUTOSAR framework from ETAS along with Elektrobit tools for this project development. Our team performed the MCAL configuration of CAN, SPI, GPIO, ADC, and PWM protocols. We also used Automotive Grade Linux (AGL) and Qt QML to build a human-machine interface (HMI) with an instrument cluster and an infotainment system to visualize what is happening inside the BMS demo.
The demo version of our battery management system was built with three separate electronics modules interconnected via CAN bus. Two of them run AGL, and one runs AUTOSAR. Data from the battery is collected and processed by the BMS board. Afterward, it is sent upon request to the instrument cluster or to the infotainment system where users can see it.
The BMS board is based on SPC58, an advanced multicore 32-bit MCU from ST, which was designed to meet the highest ASIL-D requirements for mission-critical automotive applications. The hardware also includes another ST component, an L9963E BMS IC, which can handle up to 14 cells in series, supports multiple cell chemistries, and has a built-in cell balancing algorithm and protection mechanisms.
How it works
