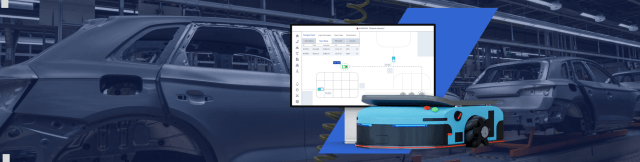
Middleware for automotive production order handling by autonomous ground vehicles
Our client is a leading German consulting company focused on the automotive industry. The company offers comprehensive IT competence and in-depth process know-how for OEMs and Tier 1 suppliers, dealers, and importers.
Сhallenge
The Tier 1 supplier's system our client aimed to automate had a complicated operations process. Our client had to be onsite to properly document all project requirements from production orders getting in via SAP ME, going through APIs and back-end logic, and finally assigning actual orders to autonomous ground vehicles on the shop floor. The client needed a scalable middleware solution to connect SAP ME and existing fleet management software to reduce manual effort.
Delivered value
We created and tested a scalable middleware solution with reusable components packed in Docker containers, which allows other Tier 1 suppliers to apply it in upcoming projects. Our back-end and front-end developers also contributed to the existing client's system by offering improvements to initial solution specifications and features to make the system even more resilient.
The process
The client initiated collaboration with Lemberg Solutions due to the lack of internal resources to develop middleware for a Tier 1 automotive supplier they serve. They needed skilled back-end, front-end, and QA engineers to create a solution that would connect the fleet management system and SAP ME.
At the start of the project, we received product specifications and a list of requested features. Since the end client’s automotive manufacturing process was unique, we had to start with a comprehensive requirements analysis. We ran a product discovery to finalize the specifications and set up a clear collaboration roadmap with a fixed budget, milestones, and deadlines.
In the course of cooperation, the Lemberg Solutions team:
- Ran requirements discovery to better understand client's business workflows
- Researched the manufacturing processes of the Tier-1 automotive manufacturer, the end user of the software, to customize the solution
- Built a middleware architecture based on reusable components packed in Docker containers
- Offered and implemented improvements to the existing software logic while working on the project
- Made the AGV order handling system more flexible by enabling real-time changes in the production configuration file
- Implemented web UI features to detect and fix order-handling issues caused by manual fulfillment
- Provided the client with a demo version every two weeks for transparent progress tracking and delivery
- Completed meticulous integration testing to ensure the middleware module reliably connected SAP ME and fleet management software
The developed middleware is now a part of the client's automotive warehouse management solution that enables production order handling. With this software, the client can help Tier 1 automotive manufacturers optimize AGV robot capacity, workforce performance, and warehouse area uses. As a result, the performance and cost efficiency at production considerably increases.
How it works
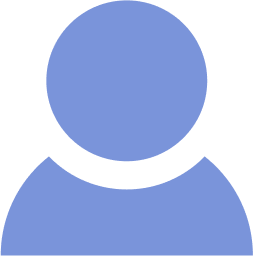
Working with Lemberg Solutions is fun and very productive. All people involved do extensively think outside the box and try to really grasp a deep function understanding which helps to identify potential problems as soon as possible. This helps the project speed immensely.
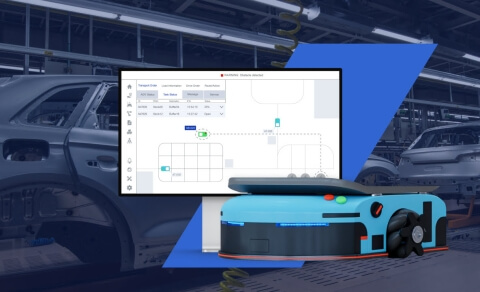