Embedded development, especially for the IoT solutions, wouldn’t get so far without lithium-ion (Li-ion) battery technology. Batteries are the power that boosts technological progress to the present day.
Our embedded engineer prepared this article to help you understand how Li-ion batteries work, including their basic principles of electrochemical cell’s functioning, and learn more about innovations in Li-ion technology. Dive in!
Why lithium-ion batteries are important
Lithium-ion batteries are widely used in electronic devices, electric vehicles, power grid storage, and other industries, including the household sector. The key reasons they are applied involve their high specific energy, energy density, cycle/calendar life, and reduced need for maintenance compared to flooded lead acid batteries [1]. Specific energy and energy density measure the maximum stored energy per unit weight or volume respectively. Lithium-ion cells have higher energy density and specific energy than historic chemistries (see Fig. 1).
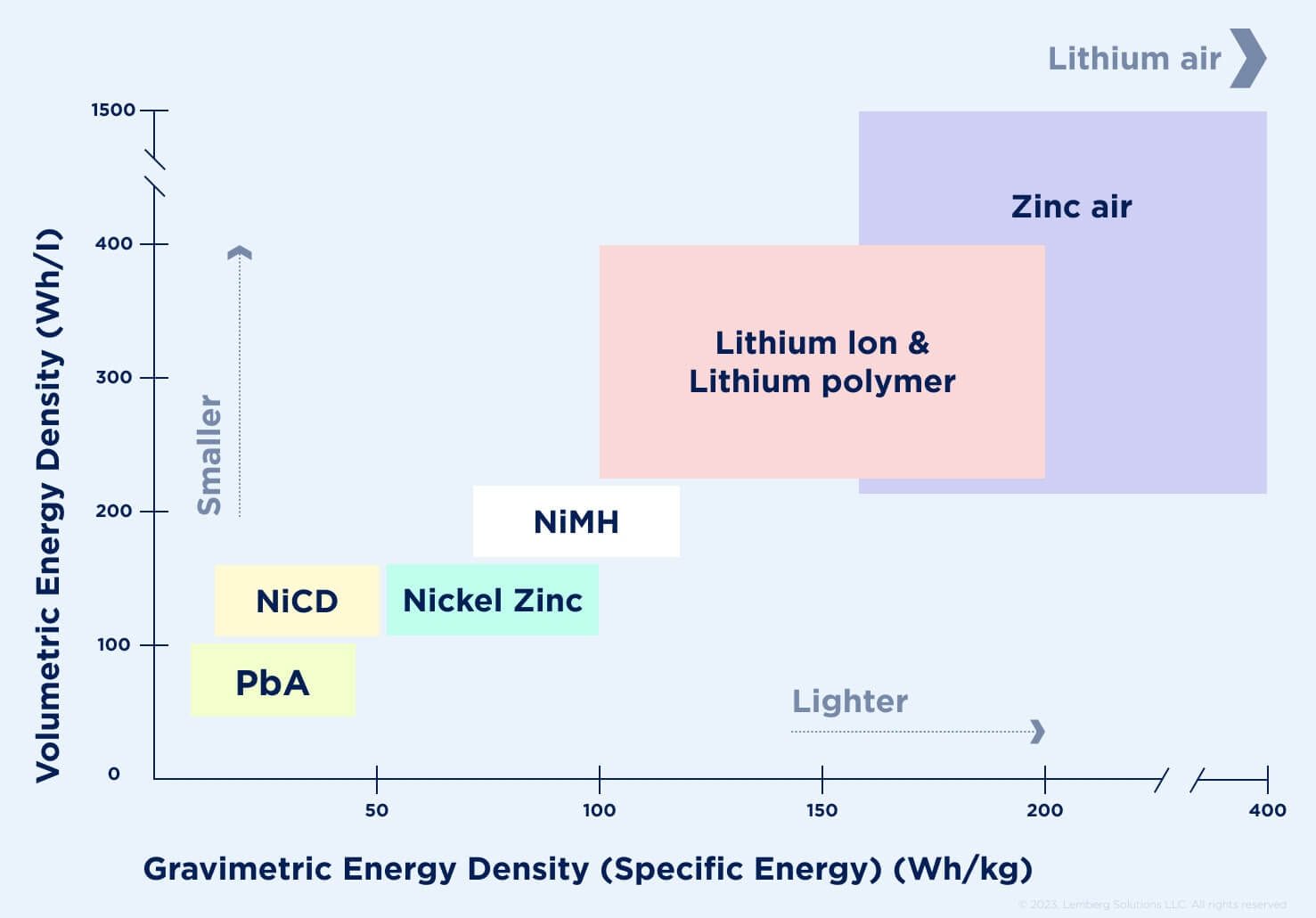
Figure 1. Specific energy and energy density for different cells [2].
Advantages of lithium-ion cells:
- higher energy density than most rechargeable cells;
- operate at higher voltages than other rechargeable cells (typically about 3.7 V for lithium-ion vs. 1.2 V for NiMH or NiCd);
- lower self-discharge rate than other types of rechargeable cells;
- long life due to a smoother intercalation mechanism in each electrode.
However, lithium-ion battery technology is currently more expensive than similar-capacity NiMH or NiCd batteries, and they are more complex to manufacture. More reactive chemicals are used in Li-ion batteries, and they tend to be less stable and require special safety precautions, such as special circuitry to protect the battery from damage due to overcharge and over-discharge.
To understand how Li-ion cells work, we will analyze the principles of electrochemical cells functioning and their development.
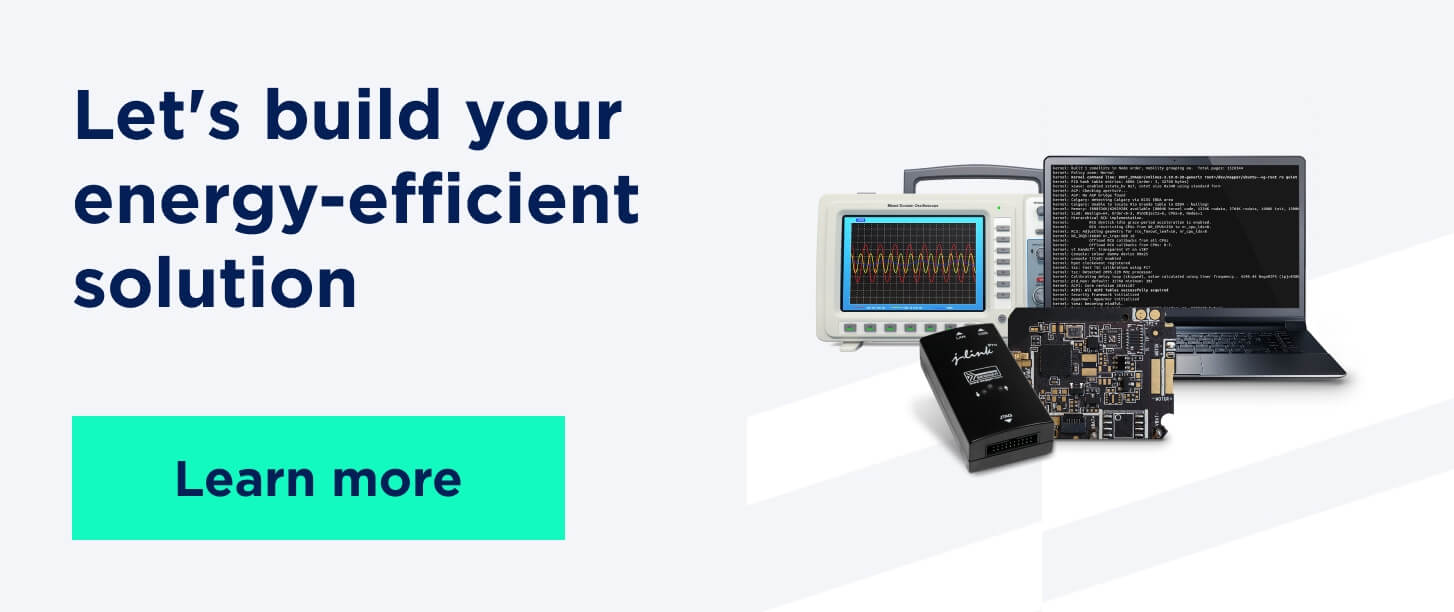
Construction of an electrochemical cell
Cells are the smallest individual electrochemical units and deliver a voltage that depends on the cell chemistry. There are primary (single-use) and secondary (rechargeable) cells. Batteries and battery packs are made up of groups of cells. For example, automotive 12V lead-acid (PbA) batteries comprise six 2V cells in series.
An electrochemical cell consists of a negative electrode, positive electrode, electrolyte, separator, and current collectors. A negative electrode is often a metal, an alloy, or hydrogen (lead metal or paste for PbA cell). During discharge, it transfers electrons to the external circuit and is oxidized. During charge, it accepts electrons from the external circuit and is reduced. A negative electrode is an anode during discharge.
A positive electrode is often made of a metallic oxide, sulfide, or oxygen (lead oxide for PbA cell). During discharge, it accepts electrons from the circuit and is reduced. During charge, it transfers electrons to an external circuit and is oxidized. A positive electrode is a cathode during discharge.
The electrolyte creates the medium for internal ion charge transfer between the electrodes (sulfuric acid for PbA cell). As electrons move in the external circuit, compensating ions must move internal to the cell. Cations are ions with a net positive charge: during discharge, they move through the electrolyte toward the positive electrode. Anions are ions with net negative charge: during discharge, they move through the electrolyte toward the negative electrode. The electrolyte is typically a solvent containing dissolved chemicals (an acid, base, or salt) providing ionic conductivity. The electrolyte must be an electronic insulator to avoid self-discharge.
The separator electrically isolates the positive and negative electrodes to avoid short circuit and self-discharge of the cell. It is often made of glass mat, fiber, polyethylene, or polymer. Since electrodes are often made of powders, current collectors are metal foils, having electrodes connected to them and conducting electrical current to cell terminals.
Battery cells store energy as electrochemical potential energy. Whenever an external circuit is completed, the electrochemical potential energy is converted to electrical energy. The negative electrode supplies electrons to the circuit, and the positive electrode sinks electrons, powering the load and discharging the battery cell. Whenever a charger provides electrical energy to the cell, that energy is stored as electrochemical potential energy to be used later. Manufacturer voltage limits must be carefully maintained to ensure safety and durability.
Constant-current/constant-voltage (CC/CV) and constant-power/constant-voltage (CP/CV) are commonly used charging methods.
The atom’s energy level is changed by gaining or losing electrons, and it is this energy that is released as electrical energy during discharge or absorbed during charge (of a secondary battery). The difference in electrical potential energy before and after a reaction can be measured as a voltage difference. The electrochemical series is a list or table of metallic elements or ions arranged according to their electrode half-reaction potentials (see Table 1).
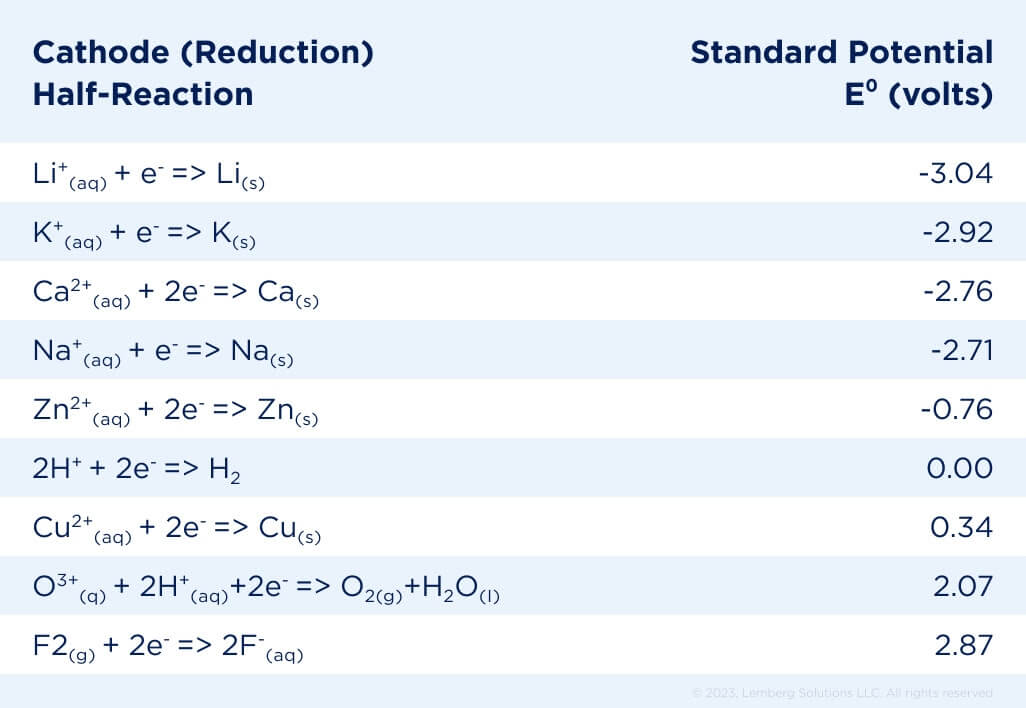
Table 1. Strengths of Oxidizing and Reducing Agents [2].
Lithium, at the top of the list, has the most negative number, indicating that it is the strongest reducing agent. Fluorine is the strongest oxidizing agent, having the largest positive value for standard potential. If we were to create a cell combining the top and bottom reactions, the cell voltage would be 5.91 V. However, there is no known electrolyte that will withstand that voltage without decomposing.
Let’s consider three electrochemical cell examples: galvanic, lead-acid, and nickel-metal-hydride.
Galvanic cell
In the negative electrode of galvanic cell (see Fig. 2), the electrolyte is ZnSO4, which dissociates into Zn2+ and SO42- when dissolved in water. In the positive electrode, the electrolyte is CuSO4, which dissociates into Cu2+ and SO42- when dissolved in water.
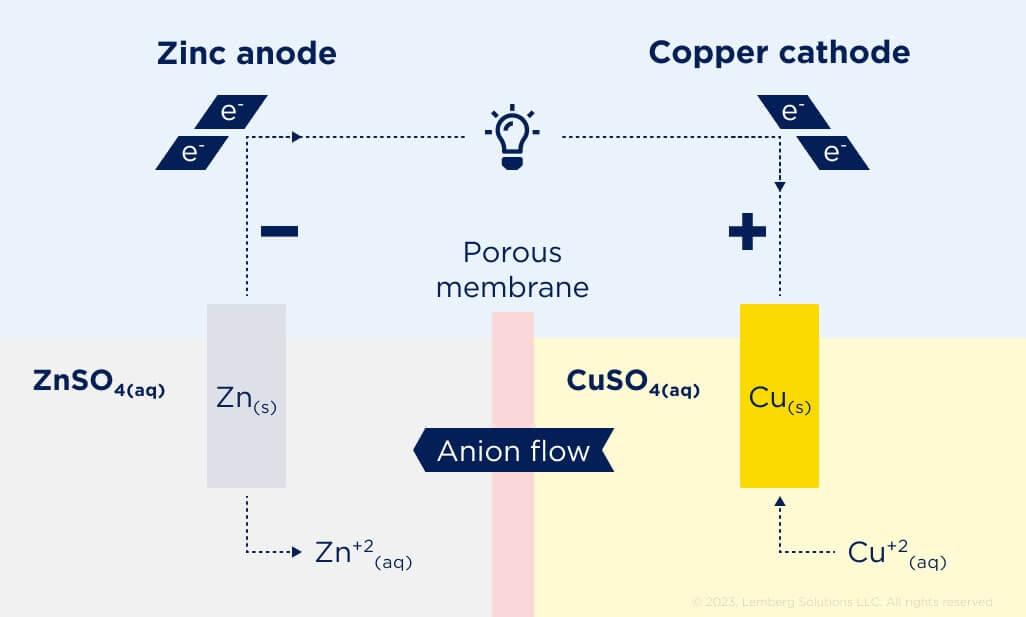
Figure 2. Galvanic cell [3].
On discharge, the zinc electrode dissolves, releasing Zn2+ into the electrolyte. The positive electrode consumes Cu2+ and copper is plated onto the copper electrode. This produces a temporary deficiency of SO42- in the negative-electrode region and a surplus in the positive-electrode region. Thus, SO42- diffuses through the porous disk from the positive-electrode region to the negative-electrode region to compensate. The opposite process happens on the charge.
At the negative electrode, we have the redox reaction Zn2+ + 2e– ↔ Zn, having standard potential E0=-0.76 V. At the positive electrode, we have the redox reaction Cu2+ + 2e– ↔ Cu, having standard potential E0=0.34 V. Overall reaction is Zn + Cu2+ ↔ Zn2+ + Cu, and it has standard potential E0 = 0.34 V – (–0.76 V) = 1.10 V.
Lead-acid cell
A lead-acid cell comprises two lead-based plates and an aqueous sulfuric-acid (H2SO4) electrolyte (see Fig.3, a). In the fully discharged state, both electrodes are PbSO4 and the electrolyte is a dilute H2SO4. The full cell has a standard potential E0 = 1.685 V – (–0.356 V) = 2.041 V.
Since electrolysis of water evolves H2 and O2 gasses, which cause bulging and deformation of sealed batteries, they need to be protected against overcharge. Additionally, batteries need to be protected against over-discharge due to the formation of lead-sulfate crystals, which often cannot be decomposed, leading to capacity loss.
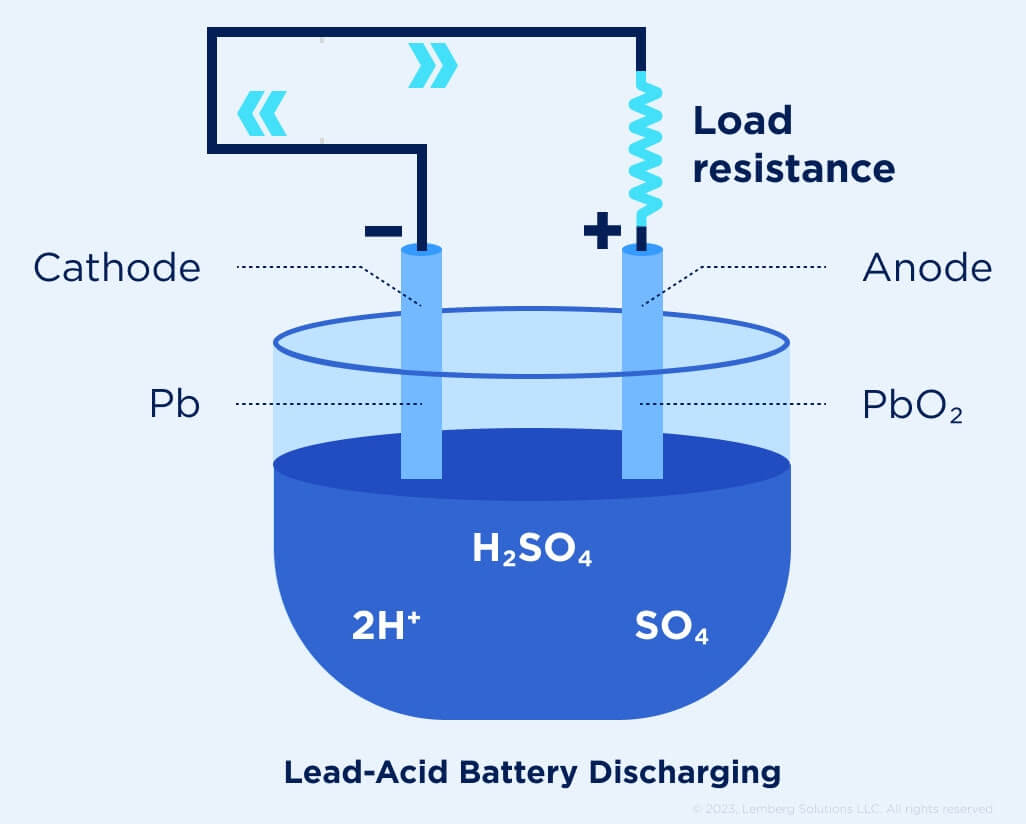
Figure 3 (a). Lead-acid cell [4]
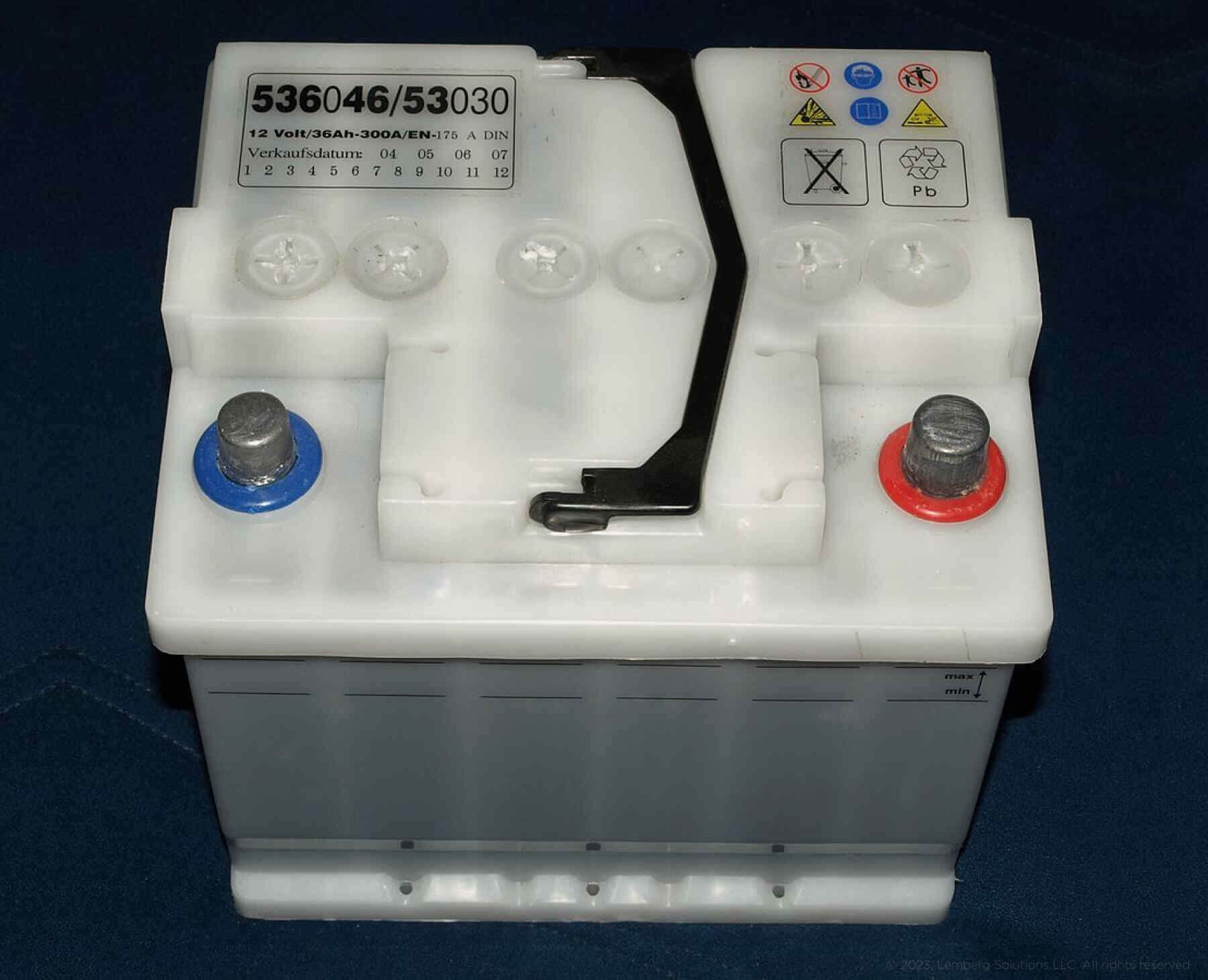
Figure 3 (b). Car battery [5]
Electrodes are usually constructed from a lead-alloy grid (for strength) covered with a sponge-like lead paste (to increase surface area and power). In “flooded” cells, the separator is a simple spacer, and the electrolyte is liquid. In “absorptive glass mat” (AGM) cells, the separator is a glass mat saturated with a minimal amount of electrolyte. Silica can be added to the electrolyte to make a gel. It also allows for sealed construction and less stratification of H2SO4 concentrations, providing longer life but lower power.
Nickel-metal-hydride cell
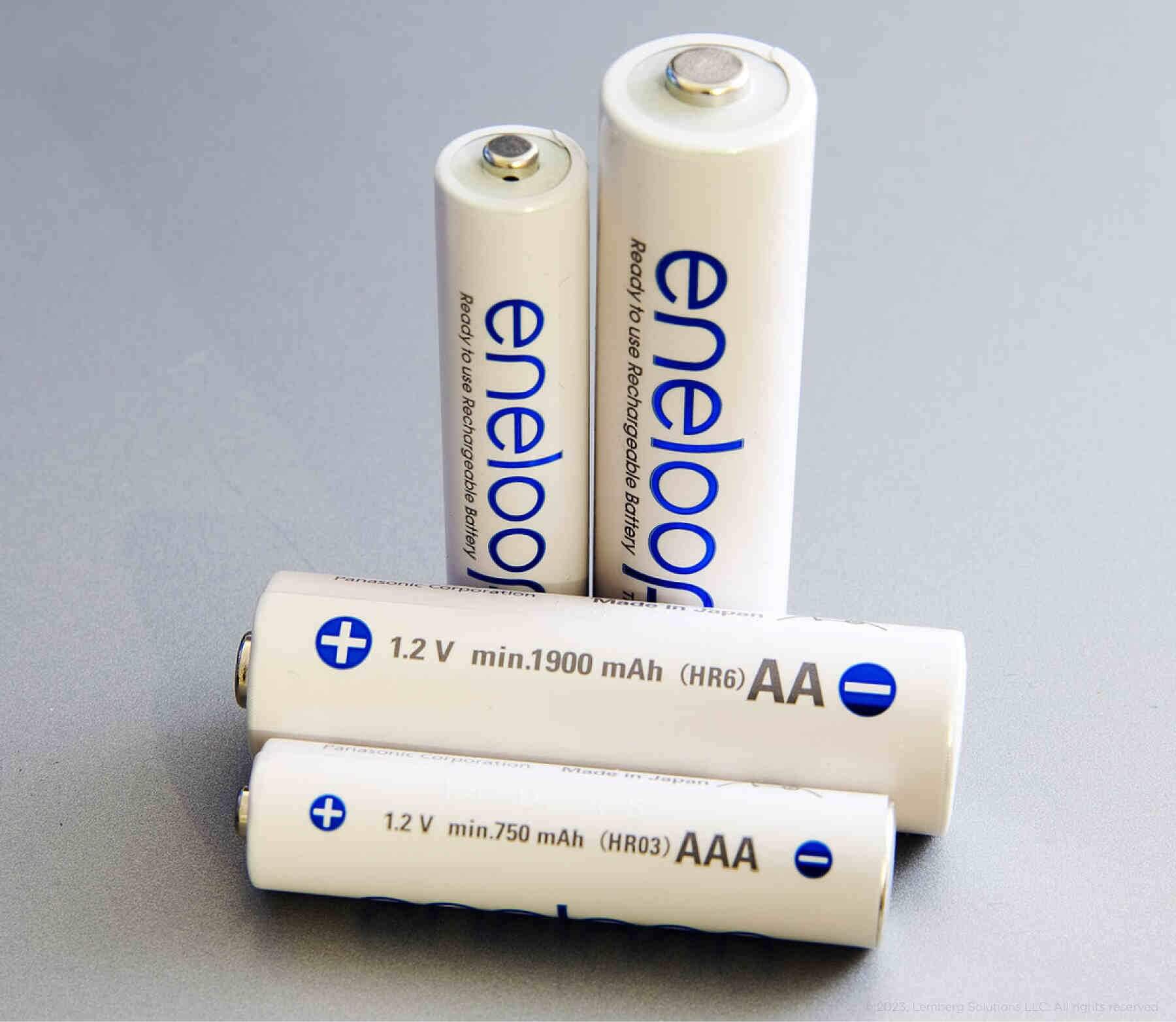
Figure 4. Nickel-metal-hydride cells [6].
Nickel-metal-hydride (NiMH) cells depend on the ability of some metallic alloys (“hydrides”) to absorb large amounts of hydrogen (like a sponge), which can reversibly react in a battery (lithium-ion cells work in a similar way). Such metals or alloys are used for the negative electrodes. The positive electrode is nickel hydroxide. The electrolyte is a hydrogen-absorbent aqueous solution, such as aqueous potassium hydroxide (KOH). It does not take part in the reaction but serves to transport the hydrogen between the electrodes. Hydrogen is absorbed into metal alloy without changing its chemical formulation or structure. It is a very gentle process (when compared with standard redox reactions) that leads to very long life of NiMH cells.
The standard potential of the NiMH cell is as follows: E0 = 0.5 V – (–0.8 V) = 1.3 V.
Care should be taken to guard against overcharge since oxygen gas is evolved when the positive electrode no longer has Ni(OH)2 left to react with OH–, but, if charged slowly, O2 diffuses and recombines safely with H+ to form water. One must also guard against over-discharge, since H2 gas is evolved.
Construction of a Li-ion cell
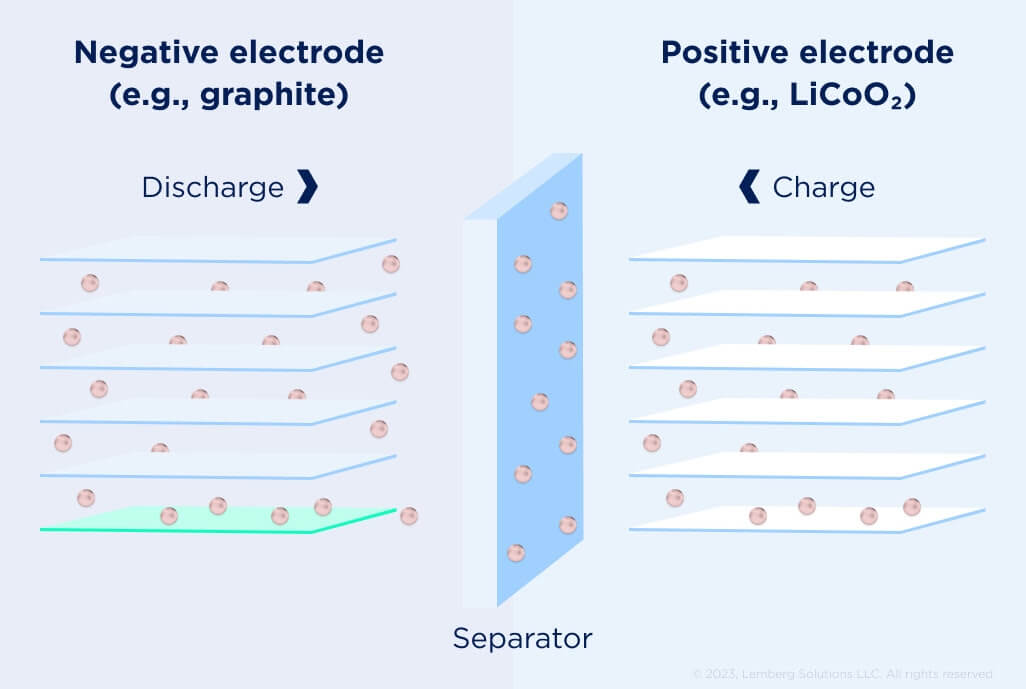
Figure 5. Components of a Li-ion cell [2].
Lithium-ion cells work quite differently from the electrochemical cells — both electrodes depend on an intercalation mechanism rather than redox reactions. Lithium is stored in the electrodes much like water is stored in a sponge, and Li+ moves through the electrolyte. Li+ enters an electrode, becoming Li when an electron is available. Li exits an electrode and becomes Li+ when it can give up an electron.
The active electrode materials are coated on both sides of metallic foils that act as the current collectors conducting the current into and out of the cell. Two basic electrode structures are used, depending on the cell form factor: a stacked structure for use in pouch cells, and a spiral wound structure for use in cylindrical/prismatic cells.
Presently, essentially all commercial lithium-ion battery technology uses some form of graphite (C6) for the negative-electrode material. The alternate negative-electrode material is LTO — Lithium titanate oxide (Li4Ti5O12), which is nearly indestructible. However, it has high open-circuit potential (making cell voltage low).
The future negative-electrode material in Li-ion cells is silicon. Using graphite, you can store up to one Li per six C atoms. Using silicon, you can store four Li per every Si atom. Therefore, energy density using silicon electrodes can be much higher. However, while volume change for a charge/discharge cycle for graphite is around 10%, it is around 400 % for silicon. Therefore, silicon electrodes tend to fracture quickly and have short lives.
Scientists at Lawrence Berkeley National Laboratory have developed a conductive polymer coating called HOS-PFM that could enable longer-lasting, more powerful lithium-ion batteries for electric vehicles [7]. The HOS-PFM coating could allow the use of electrodes containing as much as 80% silicon. Such high silicon content could increase the energy density of lithium-ion batteries by at least 30%. And because silicon is cheaper than graphite, it can provide the possibility for the production of cheaper batteries, which could significantly increase the availability of electric vehicles.
As far as positive electrodes of lithium-ion cells are concerned, the following active materials can be applied:
- Lithium cobalt oxide (LCO). In 1980, John B. Goodenough discovered that LixCoO2 was a viable material for lithium intercalation. LCO has layers, somewhat like graphite, so it is often called a “layered cathode.” LCO is commonly used in portable-electronics cells. However, this material can be challenging to use for larger projects since cobalt is rare, toxic, and expensive. Also, only about half of its theoretic capacity is usable, and the cell ages rapidly. Nickel can substitute cobalt, giving higher energy density (higher voltages at the same capacity), but it is not thermally stable.
- NCM (also known as NMC) is a blend of nickel, cobalt, and manganese (Ni, Co, Mn), which retains the layered structure and holds properties of all three constituent metals.
- NCA is a blend of nickel, cobalt, and aluminum (Ni, Co, Al).
- LixMn2O4 (LMO) was proposed as an alternate intercalation material by Goodenough and Thacker in 1983. Manganese sits in the octahedral sites, while lithium sits in the tetrahedral. This material has a cubic “spinel” structure. It allows 3D diffusion (vs. 2D for layered and 1D for olivine). LMO is cheaper and safer than LCO but can have a short lifetime due to the manganese dissolving into the electrolyte under some conditions. Additives can be added to help prevent this. However, this process is a commercial secret.
- LixFePO4 (LFP) is the most common compound from the olivine-style phosphate family — a third major category of positive-electrode material proposed by Goodenough in 1997. This material is low-cost, low-toxicity, and has low energy density because of the low open-circuit potential and low specific energy due to Fe heaviness. 1D structure tends to have high resistance, which can be partially overcome by using very small particles and including conductive additives.
The electrolyte for lithium-ion cell technology comprises salt, acid, or base dissolved in a solvent and is the medium that conducts ions between electrodes. Cells using aqueous (solvent = water) electrolytes are limited to less than 2V as water dissociates into oxygen and hydrogen when voltages are high. Since the overall voltages of lithium-ion cells are above 2V, they use electrolytes comprising non-aqueous organic solvents plus lithium salt. The most commonly used salt in lithium-ion cells is LiPF6 (Lithium hexafluorophosphate). Some other candidates include LiBF4 (lithium tetrafluoroborate) and LiClO4 (lithium perchlorate). The solvent does not participate in the (normal) chemical processes of a lithium-ion cell, but different solvents have different properties regarding aging, low-temperature performance, etc. The composition of the electrolyte is a proprietary recipe.
The separator is a permeable membrane with holes large enough to let Li+ pass through unimpeded but small enough that the negative- and positive-electrode particles do not touch each other (which would short-circuit the cell). It also serves as an electronic insulator.
Positive electrode (high potential region) uses aluminum foil as a current collector. Aluminum does not react with electrolytes if the cell voltage is above 2 V. Negative electrode (low potential region) uses copper foil, which does not react with electrolytes under similar conditions.
Cell construction processes comprise building electrode subassembly, packaging, electrolyte fill, sealing, welding, and inspection. The first stages of cell construction include the following operations: metal foils are unrolled, then a slurry of electrode solid materials is deposited on foils, dryers evaporate solvents, calendering produces desired porosity and ensures contact of active materials, and finally, foils are re-reeled in preparation for next steps.
After construction, the cell undergoes a formation cycle to grow a thin SEI layer (solid–electrolyte interphase (SEI) film layer on particles). Formation processes are proprietary (not usual CC/CV charging). A by-product of the formation cycle is a data set that enables acceptance testing and binning. Finally, cells are packaged and shipped (usually at a mid-range SOC).
Lithium-polymer differs from other battery systems in the type of electrolyte used. The original polymer design, dating back to the 1970s, used a solid (dry) polymer electrolyte that resembles a plastic-like film. This insulator allows the exchange of ions and replaces the traditional porous separator soaked with electrolyte [10]. To make the modern Li-polymer battery conductive at room temperature, manufacturers add gelled electrolytes. Most Li-ion polymer cells today incorporate a microporous separator with some moisture. Li-polymer can be built on many systems (like Li-cobalt, NMC, Li-phosphate, and Li-manganese) and is not considered a unique battery chemistry. Most Li-polymer packs are cobalt-based. However, another active material may be added.
Li-polymer cells also come in a flexible foil-type case that resembles a food package. While a standard Li-ion needs a rigid case to press the electrodes together, Li-polymer uses laminated sheets that do not need compression. A foil-type case reduces the weight by more than 20 percent over the classic hard shell. Thin film technology liberates the design as the battery can be made into any shape, fitting neatly into stylish mobile phones and tablets. Li-polymer can also be made very slim to resemble a credit card.
One more type of a Li-polymer cell is the high-voltage cell. Li-polymer cells with normal voltages are fully charged at 4.2V, while lithium high-voltage cells allow the battery to charge to higher voltage at 4.35V, 4.4V, or 4.45V. The nominal voltage of normal-voltage cells is 3.6–3.7V, while the nominal voltage of high-voltage cells is 3.8V or 3.85V. High-voltage batteries have recently started to be used in large-scale market applications [17].
John B. Goodenough made the most significant discoveries for the development of Li-ion battery technology. He was an American materials scientist and a Nobel laureate in chemistry. He developed the lithium-ion battery and the Goodenough–Kanamori rules in determining the sign of the magnetic superexchange in materials [8].
The future of batteries
The new lithium battery technology promises more energy storage and the possibility of rechargeable batteries. Read below to learn more about the future of lithium-ion batteries.
Lithium–air battery
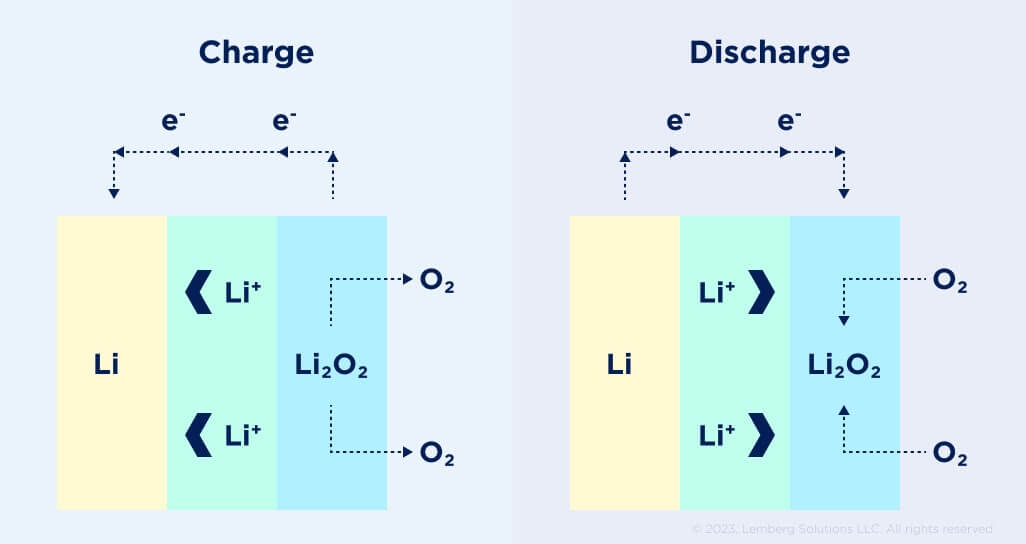
Figure 6. Schematic of lithium–air battery charge and discharge cycles [9].
The lithium–air battery (Li–air) is a metal–air electrochemical cell or battery chemistry that uses oxidation of lithium at the anode and reduction of oxygen at the cathode to induce a current flow (see Fig. 6).
Lithium-air battery provides an exciting new frontier because this battery promises to store far more energy than is possible with current lithium-ion technologies. Scientists borrowed the idea from the zinc-air battery and the fuel cell design in making the battery “breathe” air. The battery uses a catalytic air cathode that supplies oxygen, an electrolyte, and a lithium anode.
Li-air gained renewed interest in the late 2000s, partially because of advancements in material science and the endeavor to find a better battery for the electric powertrain. Depending on the materials used, the lithium-air battery produces voltages between 1.7 and 3.2V/cell. IBM, MIT, the University of California, and other research centers work on the technology [10].
As with other air-breathing batteries, the specific power may be low, especially at cold temperatures. Air purity is also a challenge as the air we breathe in our cities is not clean enough for lithium-air batteries and would need to be filtered. For all we know, the battery may end up with compressors, pumps, and filters resembling a fuel cell, consuming 30 percent of its produced energy for auxiliary support to operate.
Another problem is the "sudden death" syndrome. Lithium and oxygen form lithium peroxide films that produce a barrier, which prevents electron movement and results in an abrupt reduction in the battery's storage capacity. Scientists are experimenting with additives to prevent film formation. The cycle life will also need to be improved (lab tests currently produce only 50 cycles) [10].
Lithium–metal battery
Lithium-metal (Li-metal) battery has metallic lithium as a negative electrode (contrary to graphite in Li-ion cell). The high specific capacity of lithium metal and low redox potential make it the ideal anode material for high energy-density technologies. Rechargeable Li-metal batteries can have a long run time. Several companies and many academic research groups are currently researching and developing rechargeable Li-metal batteries as they are considered a leading pathway for development beyond lithium-ion batteries. Some rechargeable Li-metal batteries employ a liquid electrolyte, and some employ a solid-state electrolyte [11].
Lithium-metal batteries have long been seen as the future of rechargeable batteries because of their high specific energy and good loading capability. However, uncontrolled lithium deposition causes dendrite growth that induces safety hazards by penetrating the separator and resulting in an electrical short circuit.
A solution to inhibit the growth of dendrites is imminent. To produce dendrite-free deposits on Li-metal batteries, scientists conduct tests by adding nanodiamonds as an electrolyte additive. This works on the principle that lithium prefers to absorb into the surface of a diamond, leading to a uniform deposit and enhanced cycling performance. Tests have shown stable cycling for 200 hours, but more is needed for consumer applications, such as mobile phones and laptops. In conjunction with the research work, Li-metal batteries may need other precautions, including non-flammable electrolytes, safer electrode materials, and stronger separators [10].
Solid-state battery
A solid-state battery uses solid electrodes and a solid electrolyte instead of the liquid or polymer gel electrolytes found in lithium-ion or lithium polymer batteries. Solid-state batteries may solve many problems of liquid Li-ion batteries, such as flammability, limited voltage, unstable SEI formation, poor cycling performance, and durability [12].
Materials proposed for use as solid electrolytes in solid-state batteries include ceramics (e.g., oxides, sulfides, phosphates) and solid polymers. Solid-state batteries are leveraged in pacemakers, RFID, and wearable devices. These batteries are potentially safer, with higher energy densities, but cost much more.
While solid electrolytes were first discovered in the 19th century, several drawbacks prevented widespread application. Solid-state batteries tend to have high internal impedance, have poor low-temperature performance, and are subject to dendrite growth. Developments in the late 20th and early 21st century renewed the interest in solid-state battery technology, especially in the context of electric vehicles, starting in the 2010s [12].
Lithium-sulfur battery
Lithium-sulfur batteries (Li-S) offer a high specific energy of 550 Wh/kg, about three times that of Li-ion. Li-S also has a respectable specific power of 2,500 W/kg. During discharge, lithium dissolves from the anode surface and reverses itself when charging by plating back on the anode. Li-S has a cell voltage of 2.10V, offers good cold temperature discharge characteristics, and can be recharged at -60 °C. The battery is environmentally friendly.
A typical Li-ion cell has a graphite anode that hosts lithium-ions. In Li-S cells, graphite is replaced by lithium metal, a catalyst that provides double duty as an electrode and supplier of lithium ions. The Li-S battery gets rid of “dead weight” by replacing the metal oxide cathode used in a Li-ion cell with cheaper and lighter sulfur.
A challenge with lithium-sulfur cells is the limited cycle life of only 40–50 charges/discharges as sulfur is lost during cycling by distancing from the cathode and reacting with the lithium anode. Test labs now report improvements by achieving 200 cycles. Other problems are poor conductivity, a degradation of the sulfur cathode with time, and poor stability at higher temperatures [10].
As of 2021, few companies have been able to commercialize Li-S battery technology on an industrial scale. Companies like Sion Power have partnered with Airbus Defence and Space to test their lithium-sulfur battery technology. In 2022, the German company Theion claimed to introduce lithium–sulfur batteries for mobile devices in 2023 and for vehicles by 2024. In June 2023, San Jose, California, company Lyten started a pilot production line making about 100 batteries a day [13].
Sodium-ion batteries
With gradual advances in lithium-ion batteries, lithium-based material was replaced by sodium-based material in the cathode of a sodium-ion battery. Sodium ions run between the cathode and anode. However, compared with lithium ions, sodium ions have a larger volume and higher requirements regarding structural stability and the kinetic properties of materials. Sodium itself is extremely abundant and cheap. However, these batteries have lagged behind lithium-ion batteries because they have relatively low energy density.
Main characteristics of sodium-ion batteries:
- Energy density up to 160 Wh/kg;
- Fast charging (up to 80 % SOC in 15 minutes at room temperature);
- Excellent thermal stability;
- Excellent low-temperature performance (at -20 °C, the sodium-ion battery has a capacity retention rate of more than 90%);
- System integration efficiency of 80 % (weight or volume of cells versus weight or volume of battery pack);
- The cost of sodium-ion battery cells is expected to be competitive with LFP cells [14].
Graphene in batteries
Graphene is a 2D structure of graphite, a single flat layer of carbon atoms arranged into a supportive honeycomb lattice. This material has exceptional electrical conductivity and heat conductivity. The application of graphene in batteries provides large energy density and high power with less heat. Graphene can be applied to various battery technologies, including lithium, sodium, and aluminum-based batteries. In a graphene-Li-ion battery, graphene is introduced to the cathode, improving the performance and stability of the battery [15].
The graphene sodium-ion battery is another potential battery of the future. To make graphene sodium-ion batteries, researchers attach a single series of benzene molecules to the graphene to increase the spacing between the layers of graphene and enable sodium ions to enter. Ordinarily, graphene is too tightly packed for sodium ions to enter.
Solid-state graphene batteries have a semi-solid-state metallic material paired with graphene, creating a hybrid, a liquid, or graphene-carbon nanotube electrodes. The extent to which graphene batteries are solid-state depends on the engineering and design approach. The all-graphene battery is a theoretical concept that can bridge the gap between supercapacitors and lithium solid-state batteries.
Despite the advantages of graphene application in batteries, there is a significant obstacle to commercialization of graphene-containing batteries. It is complex and overly expensive to manufacture graphene. The manufacturing process isn’t mature enough for mass production — it could take a decade to mass-produce graphene-containing batteries [15].
Lithium-ion battery innovations include lithium-air, lithium-metal, solid-state, lithium-sulfur, sodium-ion, and graphene-based technologies.
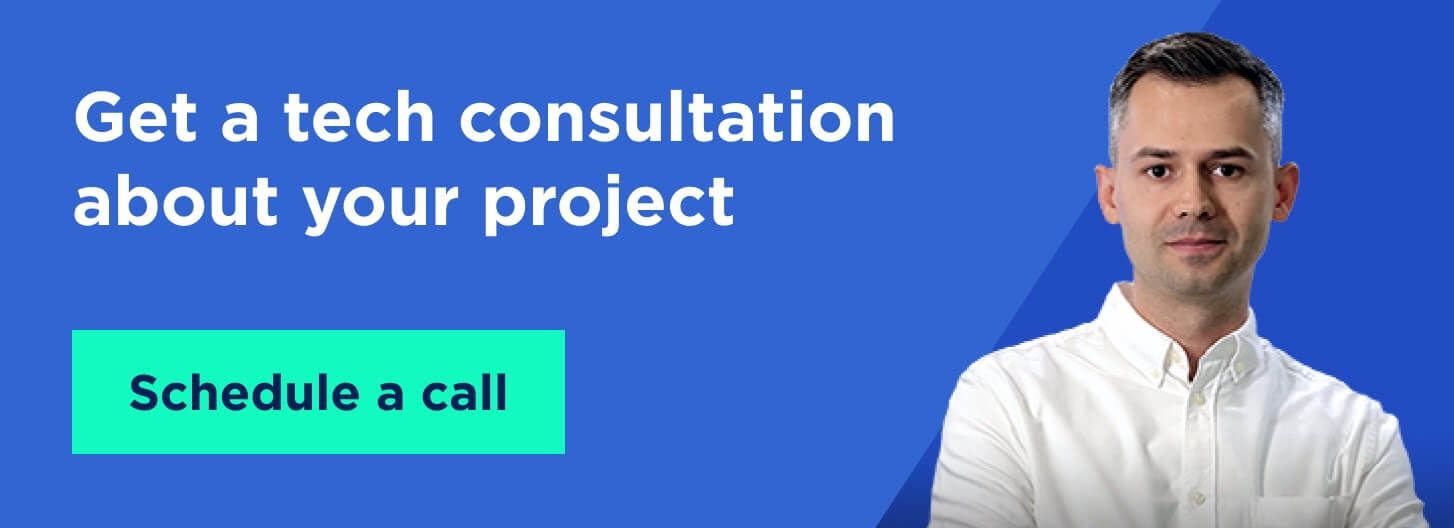
Conclusion
Lithium-ion batteries used for numerous technologies, including wireless headphones, electric vehicles, and energy storage systems undergo constant advancements. Significant improvements in lithium-ion battery technology led to a revolution in portable electronics and increased availability of battery electric vehicles. They made possible the building of power grid storage facilities over the past two decades [16]. Experimental studies of new materials and novel technologies today show promising results for the commercial production of batteries with higher specific energy, longer life, and improved safety and performance in different operating conditions. These new batteries will be a reliable source of power for many applications in the future.
If you need a tech consultation on your project, schedule a call with our experts.
Sources
- Taborelli, Carlo & Onori, Simona & Maes, Sebastien & Sveum, Peter & Al-Hallaj, Said & Khayat, Naz. (2016). Advanced battery management system design for SOC/SOH estimation for e-bikes applications. International Journal of Powertrains. 5. 325. 10.1504/IJPT.2016.081795.
- ECE4710/5710, Battery Boot Camp. Lecture notes prepared by Dr. Gregory L. Plett. University of Colorado Colorado Springs, 2011 – 2019. (http://mocha-java.uccs.edu/ECE5710/ECE5710-Notes01.pdf, accessed on September 06, 2023).
- https://en.wikipedia.org/wiki/Galvanic_cell, accessed on September 06, 2023.
- https://byjus.com/chemistry/lead-acid-battery/, accessed on September 06, 2023.
- https://commons.wikimedia.org/wiki/File:Starterbatterie.jpg, accessed on September 06, 2023.
- https://commons.wikimedia.org/wiki/File:Eneloop_6420.jpg, accessed on October 22, 2023.
- https://newscenter.lbl.gov/2023/03/07/ev-batteries-new-polymer-coating/, accessed on September 06, 2023.
- https://en.wikipedia.org/wiki/John_B._Goodenough, accessed on September 06, 2023.
- https://en.wikipedia.org/wiki/Lithium%E2%80%93air_battery, accessed on September 06, 2023.
- https://batteryuniversity.com/article/bu-212-future-batteries, accessed on September 06, 2023.
- https://en.wikipedia.org/wiki/Rechargeable_lithium_metal_battery, accessed on September 06, 2023.
- https://en.wikipedia.org/wiki/Solid-state_battery, accessed on September 06, 2023.
- https://en.wikipedia.org/wiki/Lithium%E2%80%93sulfur_battery, accessed on September 06, 2023.
- https://cleantechnica.com/2021/07/30/catl-reveals-sodium-ion-battery-with-160-wh-kg-energy-density/, accessed on September 11, 2023.
- https://topcharger.co.uk/graphene-ev-batteries-how-far-away-are-we/, accessed on September 20, 2023.
- R. Amin, N. Muralidharan, R.K. Petla, H.B. Yahia, S.A.J. Al-Hail, R. Essehli, C. Daniel, M.A. Khaleel, I. Belharouak, Research advances on cobalt-free cathodes for Li-ion batteries-the high voltage LiMn1. 5Ni0. 5o4 as an example, J. Power Sources 467 (2020) 228318.
- https://www.grepow.com/lihv-battery.html, accessed on September 20, 2023.