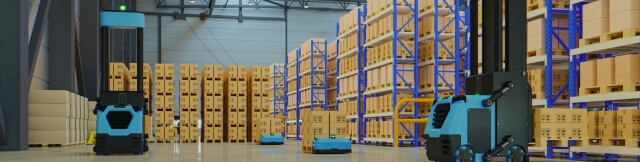
Middleware for ERP production orders handling by robotic vehicles
Our client is an international management and IT consultancy company specializing in mobility, manufacturing, transportation, and logistics for over twenty years in Germany and the USA.
The challenge
Following our previous project's success, the client approached us to develop a middleware module for operating two types of AGVs in warehouses. This solution should operate as an endpoint from the end customer to our client’s system and include a particular AGV loading logic.
Delivered value
We quickly gathered a team with relevant experience so the client could elaborate the project specification and kick off development right away. Due to our efficient clarification of requirements, suggestion of a realistic timeline, and clear scope, the client received the middleware module on time.
The process
At the initial stage, we proposed several options on how robots could optimally pick up boxes and deliver them to points in the warehouse. To create a robust and cost-effective solution, our engineering team considered the following parameters:
- Box size
- Delivery priority
- Distance to the station and between the stations
- Conveyor layer
- Loading sequence.
After the client approved the most suitable solution, we developed a roadmap and defined the project scope, including the clear delivery date and total project cost.
We divided the development into two milestones for different types of vehicles, followed by accessibility testing and production support. Throughout the development process, we were responsive to changes in requirements and tracked them to ensure a transparent workflow. Each week, our engineering team had a call with the client to discuss updates, progress, and any issues or questions.
As part of the project, we customized the AGV configuration to suit different warehouses and their variations of robots. Our team also developed an application for operators that allows them to keep records, search orders, validate data, and monitor everything in real time without manual interaction with a display.
To correct errors in the early development stage, we created a test environment that simulated actual operating conditions and used data to conduct various types of testing.
We integrated the middleware module with both sides: the ERP system on the end-customer side at a warehouse and our client’s fleet management system. Now, the client is getting ready to launch the solution into the market and start a new development project with our engineering team.
How it works
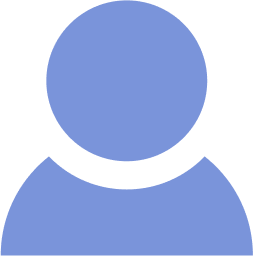
Working with Lemberg Solutions is fun and very productive. All people involved do extensively think outside the box and try to really grasp a deep function understanding which helps to identify potential problems as soon as possible. This helps the project speed immensely.
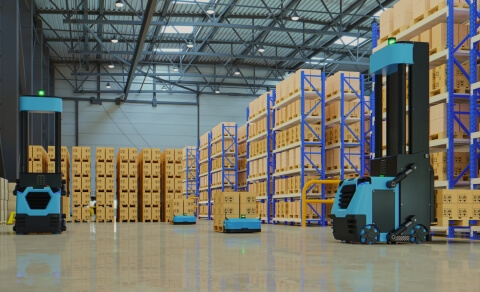