Predictive maintenance based on ML models is gaining popularity among manufacturers since it helps to reduce maintenance costs. With the help of AI, data science engineers can build a predictive maintenance system that anticipates numerous failures and allows business owners to fix them before equipment downtime. It is especially important if manufacturers don’t have the needed equipment parts when an issue arises.
According to Deloitte, predictive maintenance decreases unexpected breakdowns by 70%, boosts productivity by 25%, and reduces maintenance costs by 25%. That is why it is important to integrate an effective predictive maintenance system into your solution.
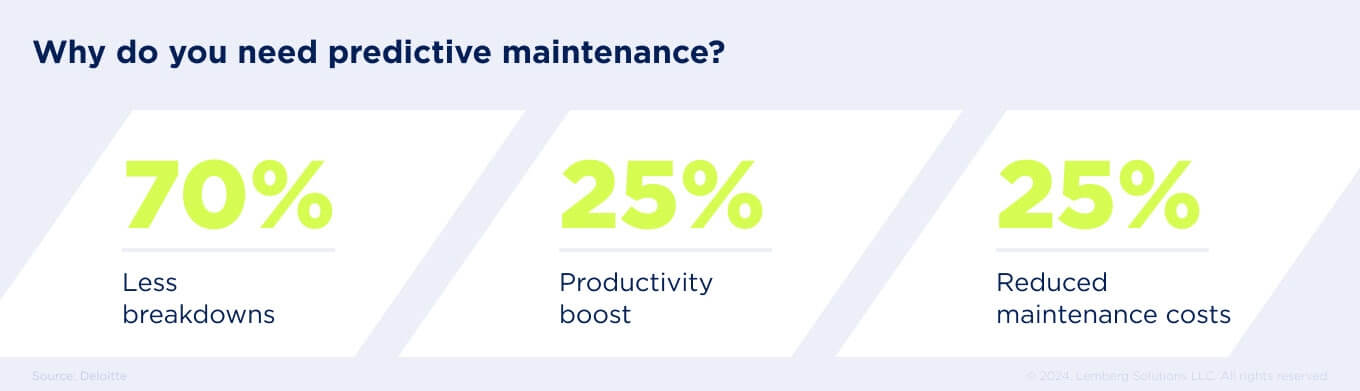
In this article, we explore real-life use cases of predictive maintenance systems, the best algorithms, how to implement the system on our real project, and development challenges. Dive in!
What is predictive maintenance?
Predictive maintenance is an effective approach to improving system performance and decreasing equipment downtime. It runs specific data analysis to forecast any system failure before it happens. This way, a company has enough time to intervene and fix the problems, which saves expenses and time for replacing broken equipment.
Predictive maintenance helps to detect possible issues by analyzing data and using it to predict the next issue. In some cases, predictive maintenance may be used to identify the reason of the issue. The companies can avoid unplanned disruptions and devote more time to business operations and system improvements.
There are three main types of system maintenance: corrective, preventative, and predetermined:
Corrective maintenance is a type of maintenance that occurs when a breakdown has already happened. This type is often used for low-value equipment that can be quickly fixed or changed (e.g., light bulbs). Corrective maintenance can be applied for systems that don’t have a significant impact on business operations if they malfunction.
Preventative maintenance focuses on pre-scheduled checking of a system’s performance to prevent any unexpected failure. Businesses usually leverage this type of maintenance for moderately valued equipment. Preventive maintenance occurs outside of production hours.
Predetermined maintenance revolves around predicting potential failures without relying on any prescheduled maintenance. Predetermined maintenance allows businesses to estimate how long the equipment will run. This type of maintenance helps to take care of expensive equipment.
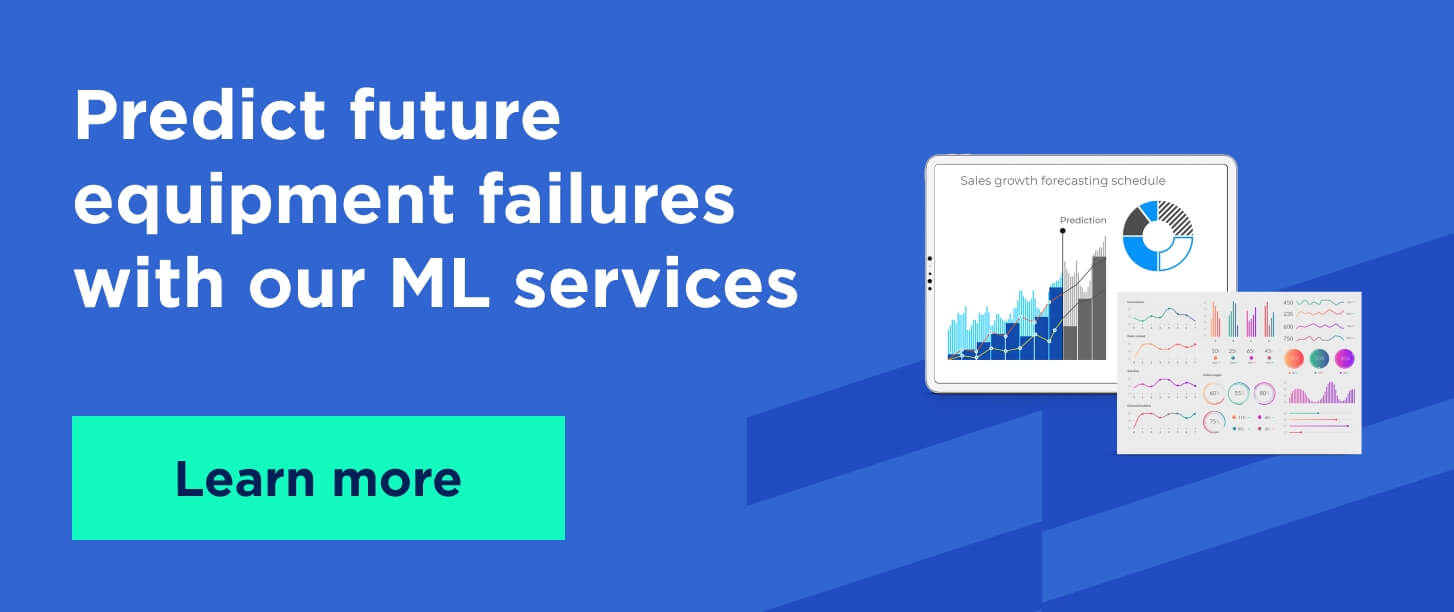
Real-life use cases of ML for predictive maintenance
ML models can make prediction maintenance more effective by increasing the accuracy of predictions. Read below to learn how companies embrace machine learning for predictive maintenance.
Solar power plants
A predictive maintenance system operating with ML models is efficient for solar power plants. Manufacturers pay special attention to solar inverters, which convert the energy generated by solar panels into the energy used by power grids. Data science engineers collect historical data on weather conditions and normal solar inverter performance. Using this data, they create an ML algorithm that detects any anomalies in the solar inverter’s behavior and notifies the manufacturers about the issue a week before it breaks down the system.
Data scientists can create predictive maintenance systems that would detect anomalies and identify the cause of the issues.
Equipment maintenance
Manufacturing companies can leverage machine learning-based predictive maintenance solutions to predict any equipment failures and prevent them in a timely manner. To do so, a company can integrate sensors into the production equipment to monitor its performance. The sensors collect historical data and provide a clearer picture of equipment work and issues.
In this case, historical data helps data science engineers build an ML model that can predict when equipment failure may occur and why. The historical data from the sensors ensures that as many issues as possible have been identified. This way, the ML model will provide more accurate and timely results.
ML algorithms for predictive maintenance
Data science engineers usually develop machine learning predictive maintenance with the help of regression algorithms and time serial models. Read below to learn more about their approaches.
Regression algorithms
ML algorithms include regression algorithms that establish a correlation between independent and dependent variables. In terms of predictive maintenance, regression algorithms help to build such a correlation between equipment and maintenance requirements. Working with regression models, data science engineers apply historical data to develop ML models that will accurately predict equipment failures.
The data science team can establish linear and non-linear relationships between the dependent and independent variables. To visualize the data and understand how the model operates, they develop a scatter plot (a random set of values) to determine if they correlate with each other. Data science engineers can also leverage residuals (a distinction between predicted results and the data) to ensure that the predictions are accurate.
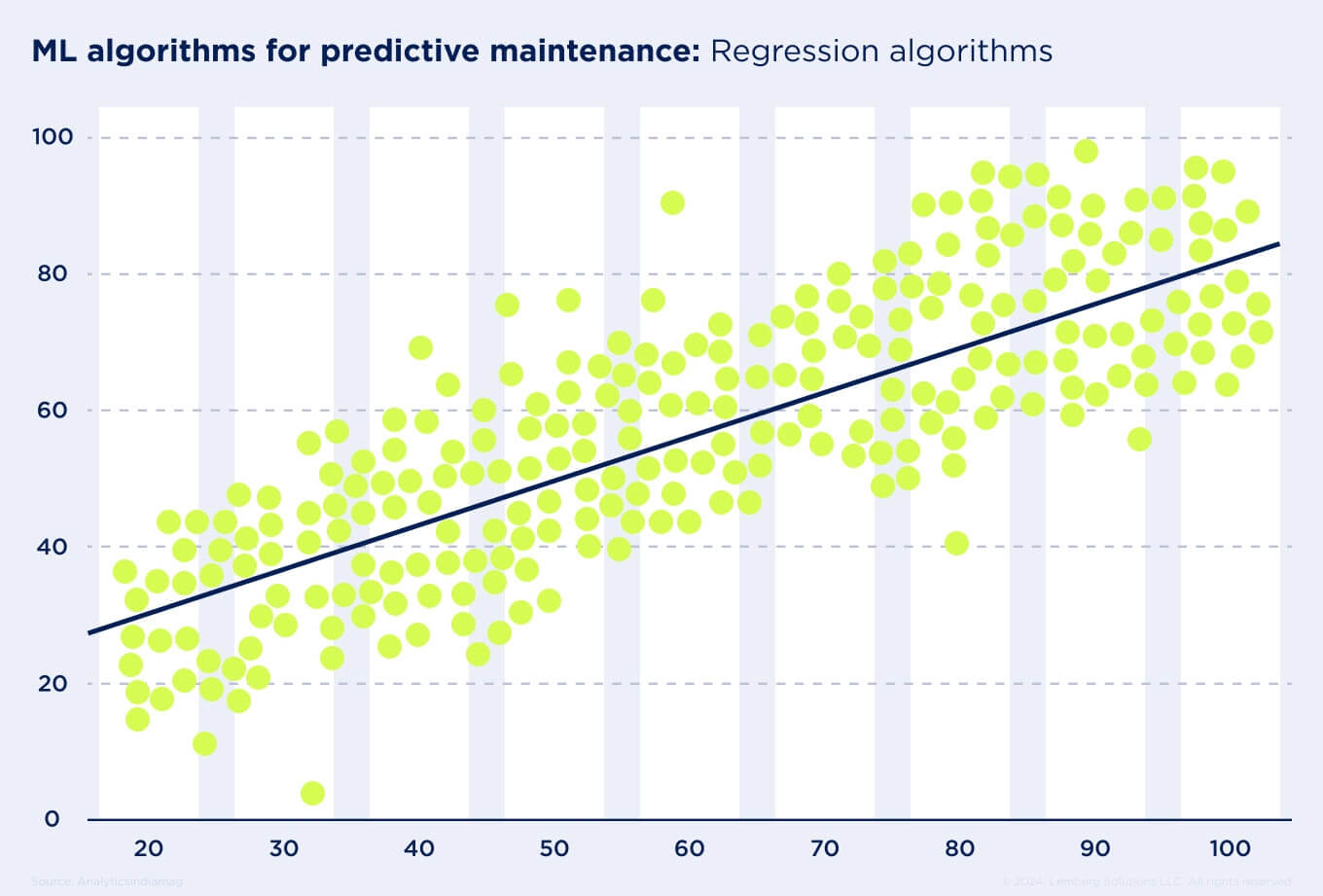
Time serial models
Time series predictions are also popular since companies often depend on time when needing to predict and prevent certain failures. Time serial models predict future events using the time component and historical data. Machine learning predictive maintenance revolves around evaluating the possibility of future events based on previous failures. With time serial models, the data science team can analyze the sequence of events in different periods of time. They estimate historical data and establish time patterns to make predictions accurate and timely.
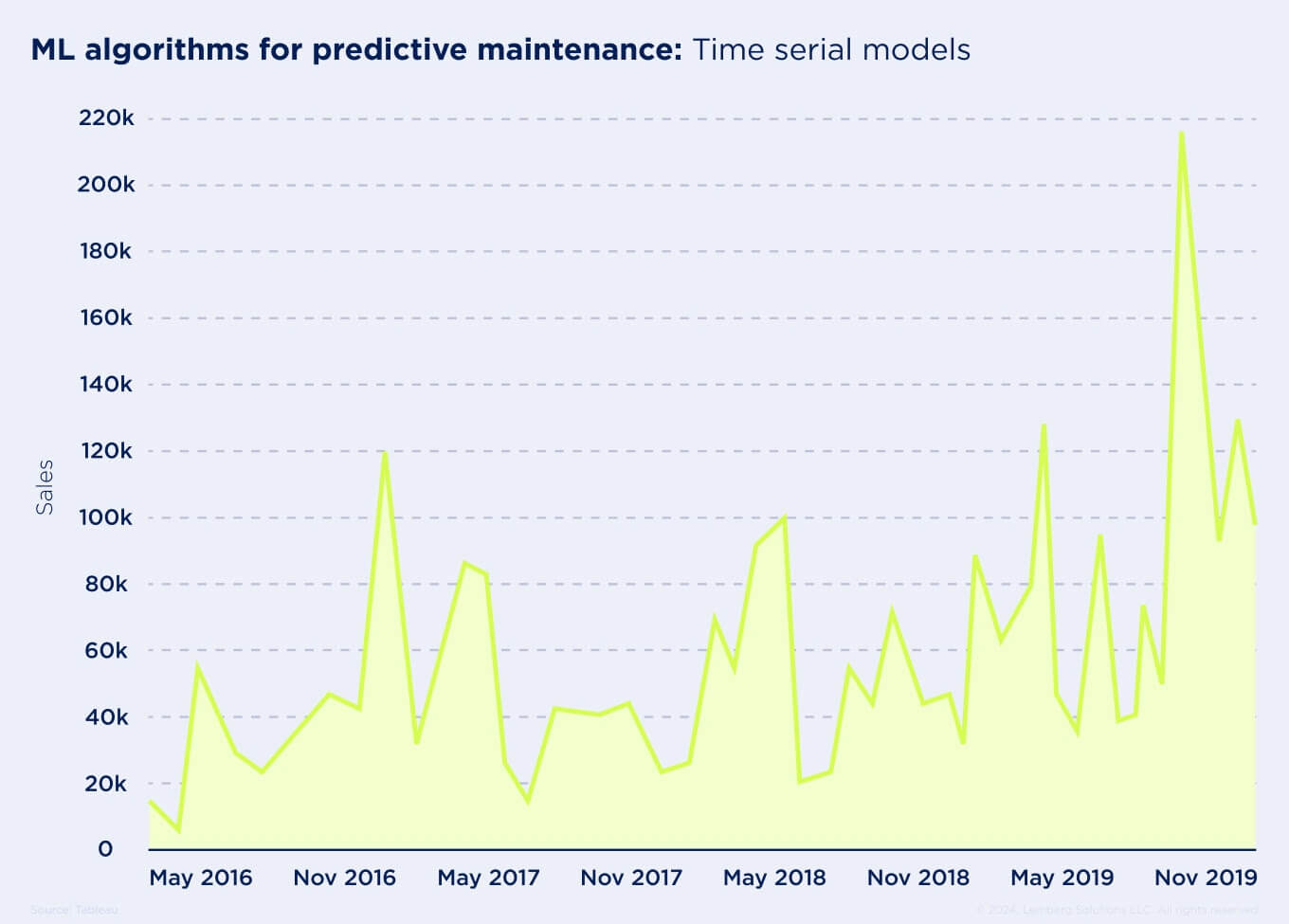
To ensure an accurate predictive maintenance system, learn about other data science services and methods.
How to implement ML for predictive maintenance: our use case
There are two common approaches to building a predictive maintenance solution. One includes the usage of historical data, while another — anomaly detection.
The historical data approach is the most reliable since it is based on data about the system’s normal performance and breakdowns. With this approach, data science engineers can identify the events when a system is close to failure and train an ML model to focus on those events. As a result, the model will predict a failure in advance, which provides enough time to resolve the issue and avoid any system downtime.
An anomaly detection approach relies on the data about the system’s normal performance. The data science team uses the data without any information on failures and trains an ML model to detect anomalies (any deviations from normal performance). An anomaly detection approach is useful for innovative systems that undergo field testing. An ML model will detect any anomalies and provide data on system failures, which can be used for further model training and improvement.
Wind turbine predictive maintenance system
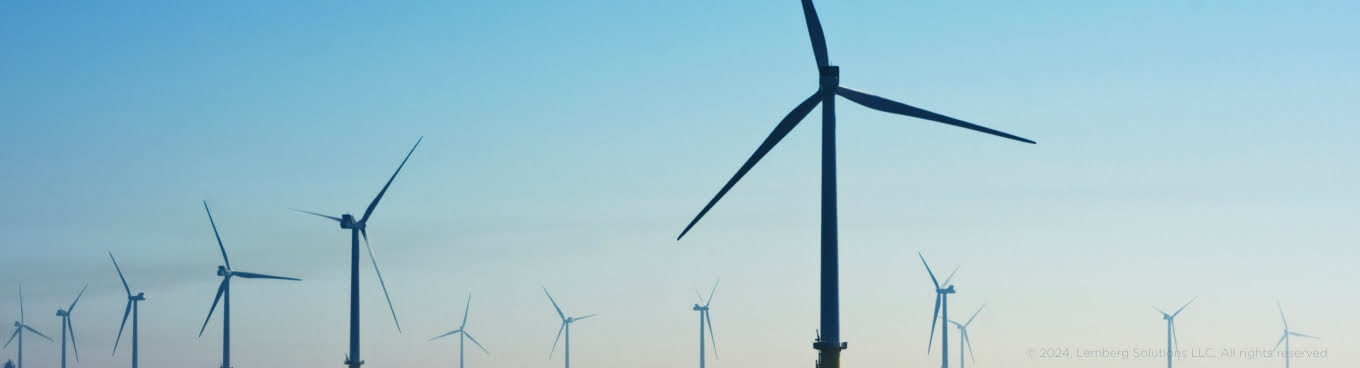
Our data science team developed a machine learning-based predictive maintenance system to prevent wind turbine failures. The client provided us with historical data for the whole year of turbine performance monitored by sensors.
In this case, our data engineers chose a combined approach of historical data and anomaly detection. They created a dataset with normal system behavior through all seasons and different weather conditions. This way, an ML model could analyze whether the system’s performance deviated from normal behavior under different circumstances.
Note that the anomaly detection approach worked in this case because the data science team used historical data, including numerous variations of the turbine’s normal behavior. If historical data have only covered two of four seasons, an ML model wouldn’t provide so accurate results.
With our system, the client managed to decrease their maintenance costs to 47%. Moreover, they could receive predictions as early as 48 hours before a system failure. However, if the client requires an earlier prediction time, our data science team will retrain the model for other prediction time.
Check out more details on this project development.
If you don’t know how to implement machine learning for predictive maintenance of your solution, don’t hesitate to consult with our data science team.
Challenges of predictive maintenance model development
Predictive maintenance using machine learning can lead to certain challenges, such as accuracy of failure detection, timeliness of predictions, and data security. Learn why these challenges arise and how data science engineers deal with them.
Accuracy of failure detection
Even though historical data proves to be helpful in increasing the accuracy of an ML model, it cannot cover all possible failure cases. Historical data includes a variety of failure information for a specific period of time. However, some failures can occur after the predictive maintenance system has been developed.
Data science engineers can train the model to detect known failures and anomalies that deviate from normal system behavior but haven’t been identified as failures yet. This way, businesses can still know that something is wrong. The data science team supporting the solution can retrain the model and add new failure cases when they arise.
Timeliness of predictions
A predictive maintenance system ensures that business owners have enough time to prevent system failure since it reports the issue before the breakdown occurs. However, some equipment requires more time to fix it. For example, if some equipment parts are out of stock, a business owner must wait a week or more to order them. Thus, the earlier a system reports a potential issue, the better.
Sometimes, a predictive maintenance system won’t detect an issue early enough for a business owner to avoid any downtime. But in most cases, such systems provide enough time for timely maintenance.
Data security
Predictive maintenance systems monitor large amounts of private data. Companies need to ensure that their systems are encrypted to avoid any data leakage. Besides, they need to set up secure data storage for their solutions. To maintain data security, companies need to restrict access to predictive maintenance data and carefully choose a tech vendor who develops the system.
Data science engineers at Lemberg Solutions strictly follow international data security regulations since our company has obtained ISO 9001:2015 and ISO 27001:2013 certifications.
Predictive maintenance trends
Apart from ML systems, predictive maintenance can be performed by thermal imagers, ultrasonic acoustic detectors, and digital twin simulators. All these solutions can also be enhanced with ML models to improve data analysis and make better predictions.
Infrared thermographic analysis
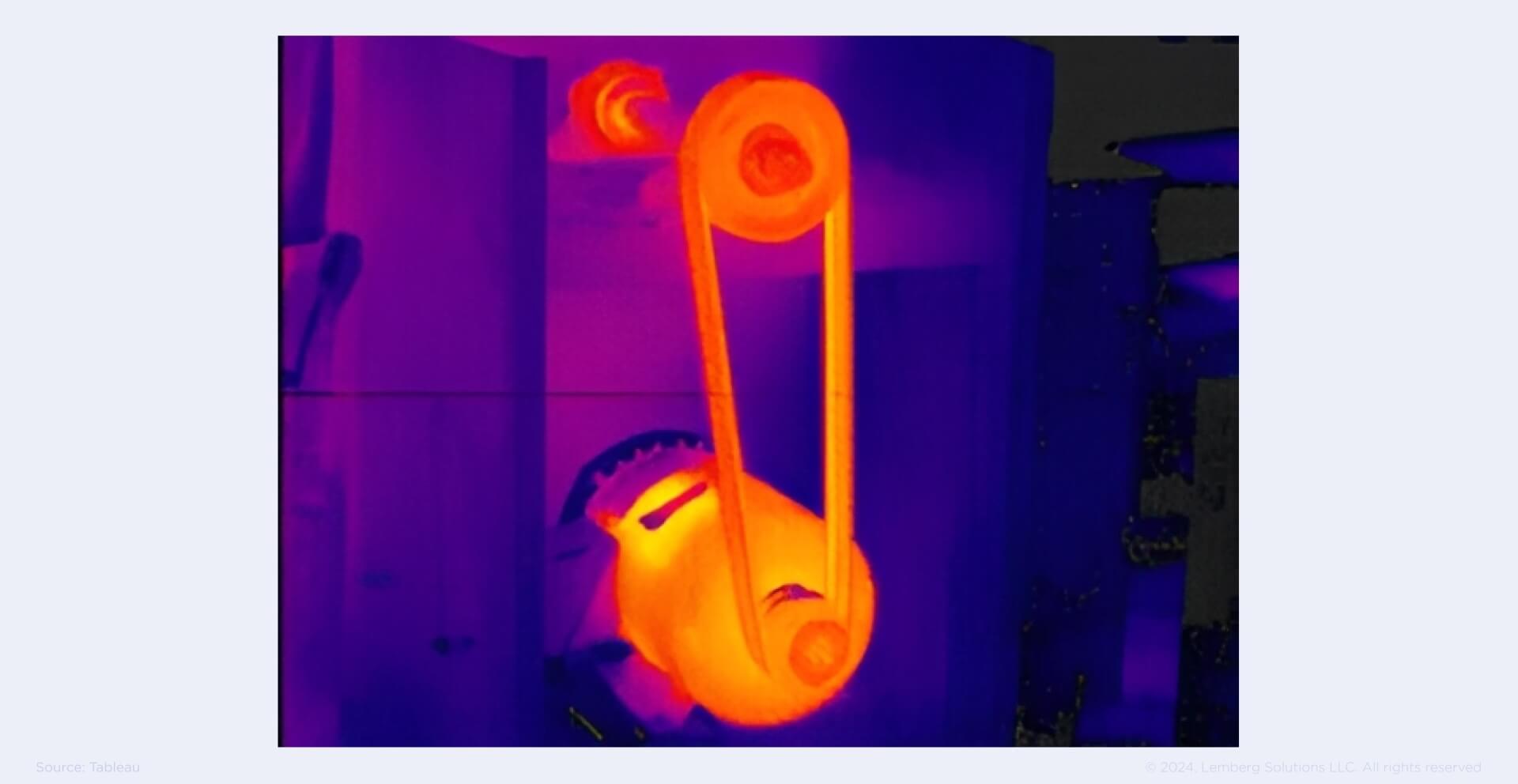
Infrared thermographic analysis focuses on collecting temperature measurements of different equipment parts to make sure they run smoothly. A thermal imager provides two-dimensional images with temperature results of separate parts and a piece of equipment as a whole. This way, manufacturers get more information about equipment condition and can establish better maintenance plan.
Ultrasonic predictive maintenance
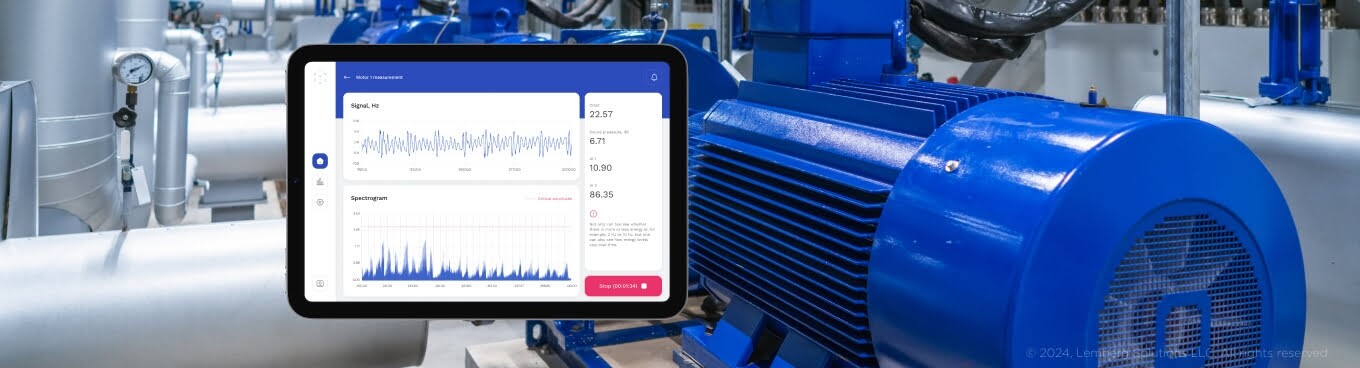
Manufacturers can apply ultrasonic acoustic detectors to check equipment condition using the sound. This is an easy-to-use technology that helps recognize any failures and equipment wearing.
Such detectors are efficient for condition-based monitoring of rolling bearings. Manufacturing equipment makes friction sounds inaudible to human ears. Those sounds define whether rolling bearings operate normally or need to be replaced.
Our embedded team created an ultrasonic device for monitoring rolling bearing condition. Read more here.
Digital twins
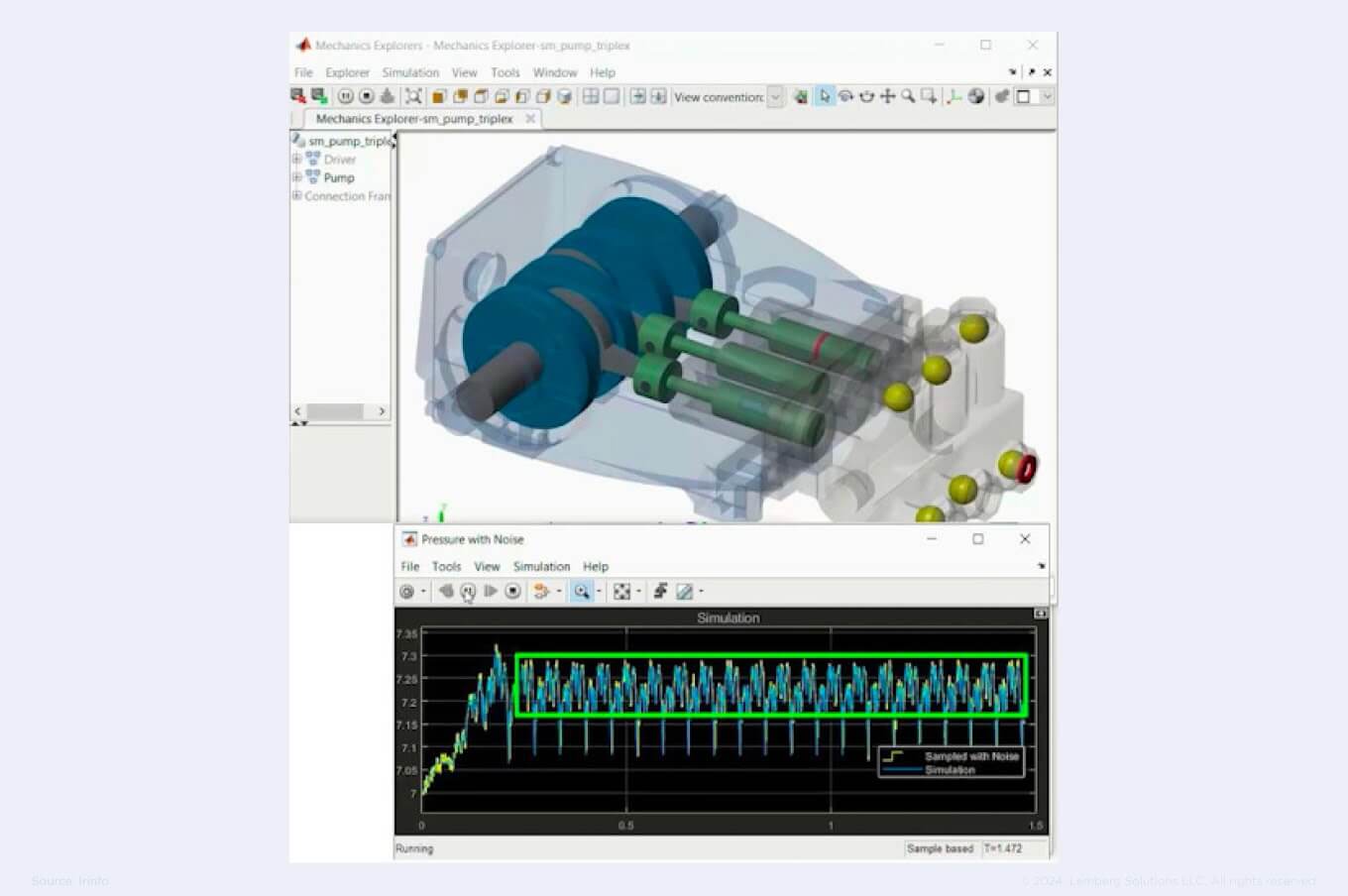
In some cases, manufacturers cannot collect data from physical equipment during its breakdown. To cause failure on purpose for data collection may lead to permanent damage and money losses. That's when digital twins come in handy. A digital twin is a piece of needed physical equipment recreated in a digital environment. A digital twin can mimic the reaction of real equipment during its breakdown. Manufacturers can collect the needed data from a digital twin to understand what issues to prevent in the future.
In the image, you can see a digital twin pump created with the help of Simscape, MATLAB, and Simulink. When the needed data is collected, data science engineers train an ML algorithm on simulation data to predict similar failures.
Vibration analysis with accelerometers
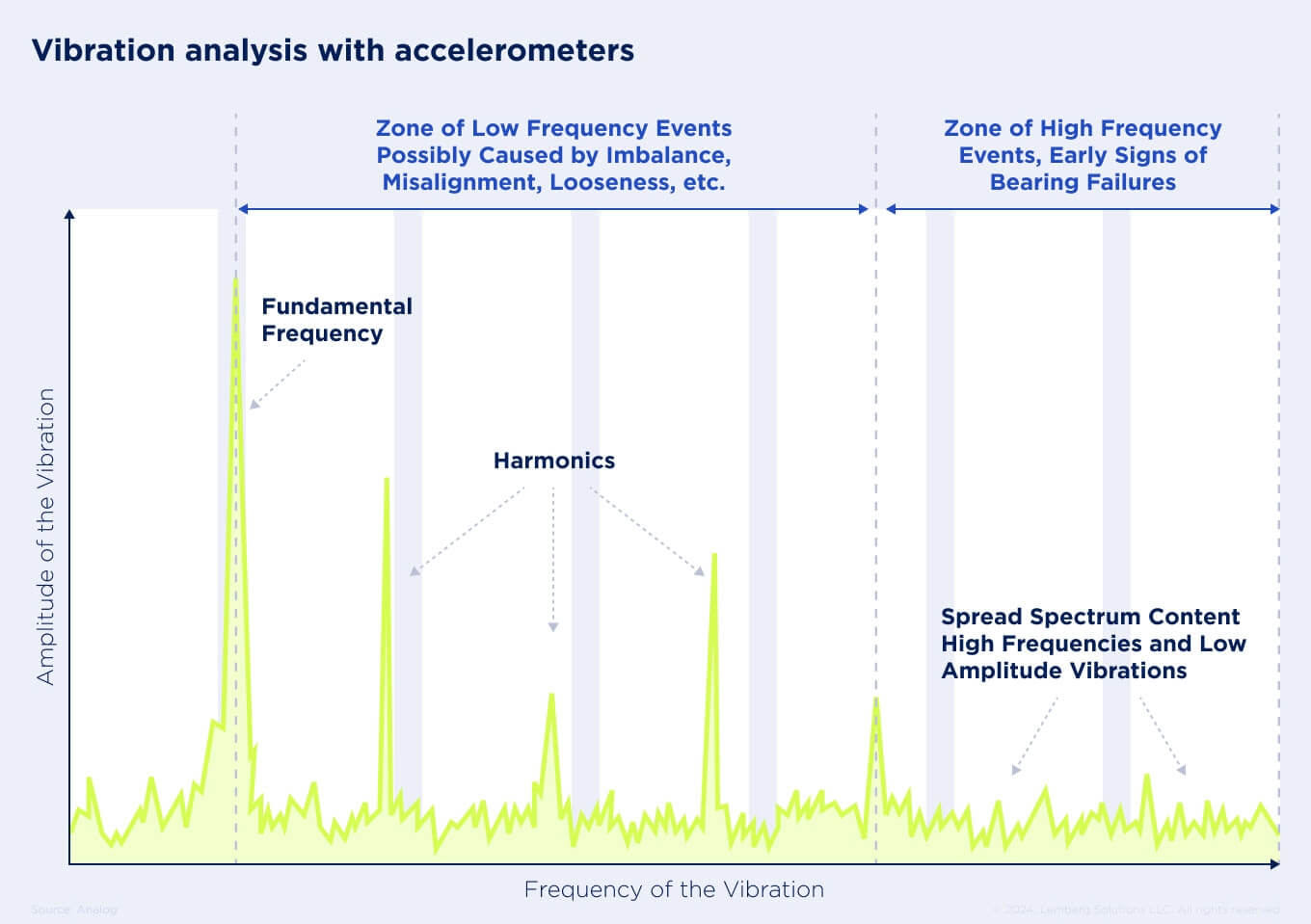
To measure the condition of the rotating equipment, accelerometers that analyze vibration can work best. If the accelerometer recognizes unusual vibrations, it means that there is an issue with a rolling mechanism, such as wearing, imbalance, and so on. The manufacturers use accelerometer data to understand whether equipment requires a checkup or replacement. This device is usually placed near the equipment that needs to be monitored.
Wrapup
Machine learning algorithms for predictive maintenance are the most helpful tools when it comes to anticipating possible equipment failures. The future of predictive maintenance is closely linked to the use of ML models since they can analyze large amounts of real-time data. Manufacturers who integrate ML-based predictive maintenance into their solutions reduce the number of unexpected failures, downtime, and cost losses.
Need to develop a predictive maintenance algorithm to anticipate your equipment breakdowns? Our data science engineers can help! Get in touch and tell us about your needs.
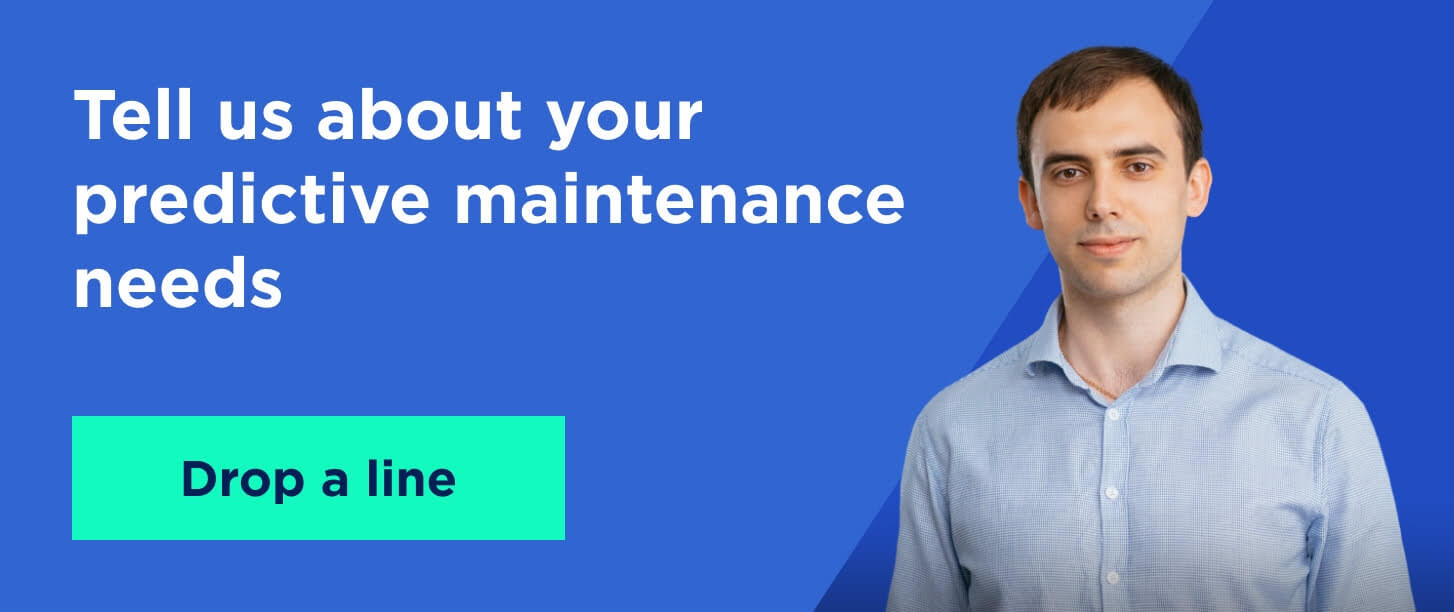
FAQ
How do ML algorithms contribute to predictive maintenance?
ML significantly enhances predictive maintenance by helping to analyze historical data and identify anomalies. ML models can predict equipment failures or maintenance needs before they occur, enabling organizations to schedule maintenance activities beforehand. This approach helps minimize downtime, reduce maintenance costs, and optimize the overall efficiency of equipment and systems.
What types of data are required for effective ML-based predictive maintenance?
ML-based predictive maintenance relies on various types of data to train accurate models. Commonly used data includes sensor data, historical maintenance records, and environmental conditions. Integrating data from diverse sources helps ML models understand normal operating conditions and detect deviations that may indicate potential failures. Additionally, real-time data enhances the accuracy of predictions and enables timely interventions to prevent equipment failures.
How can organizations implement ML-based predictive maintenance in their operations?
Implementing ML-based predictive maintenance involves several key steps. First, organizations need to gather relevant data from their equipment and systems. To do so, companies may need to integrate sensors into their equipment and collect historical maintenance records. Second, companies can provide this data to a data science team for further processing and model deployment. Moreover, continuous monitoring and model refinement are essential for maintaining accuracy over time.