IoT drives the digital transformation of traditional manufacturing processes by introducing remote process monitoring, wearable technology, digital twins, and artificial intelligence. These tech advancements help businesses achieve higher productivity, cost reduction, and proper machinery management.
This article will cover how IoT keeps revolutionizing manufacturing, what applications it has found, and what tech trends to expect. Let's explore the production process shifts powered by IoT together.
What is the Internet of Things in the manufacturing industry?
IoT, known as industrial IoT in manufacturing, is a noteworthy step in the digital transformation of production processes, making them automated, safe, quicker, and more efficient. Manufacturing is one of the top growing industries worldwide, where more than 125.6 million devices will be connected via IoT in 2024.
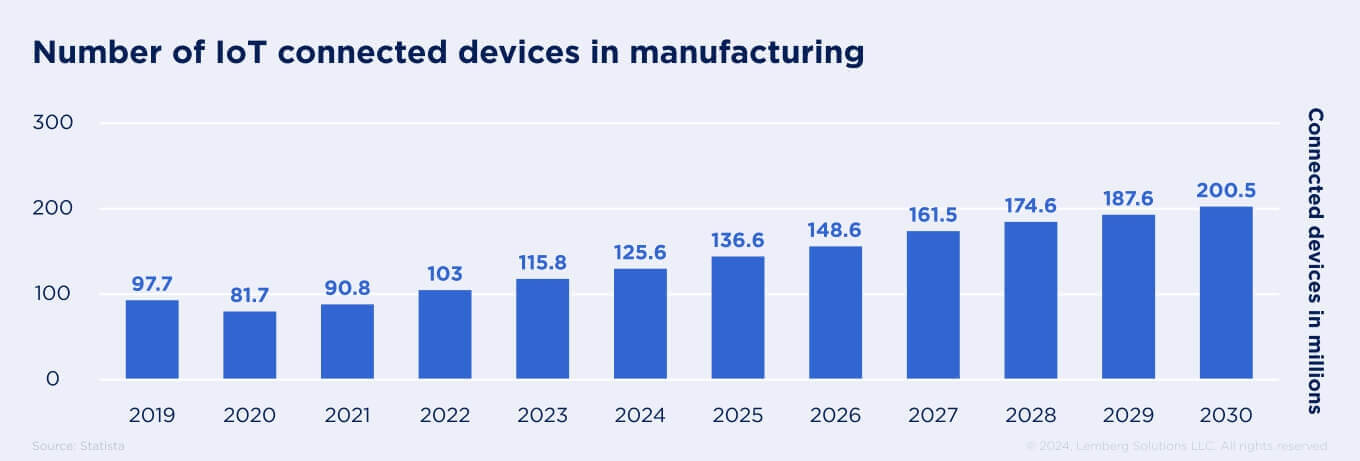
Thanks to real-time monitoring and data collection and analysis at each manufacturing stage, you access the full-fledged picture of your company processes and can find improvement areas based on the valuable data insights from the working environment.
Among the primary reasons manufacturers want to adopt IoT are resource optimization, securing their data used within internal digital systems, and decreasing energy consumption. That's why IoT finds more and more applications in manufacturing, as 28% of companies worldwide are willing to invest more in industrial automation-based process control, condition-based equipment, energy management systems, and AI-based solutions.
IoT in manufacturing industry: use cases and applications
IoT transforms the production environment by making it smart, safer, and more effective. This technology keeps evolving within the manufacturing industry, where companies are projected to integrate 1.1 times more devices with IoT sensors in 2024 (approximately 17 mln devices) compared to the previous year (15 mln devices).
As of today, we highlight digital twins, AI-based predictive maintenance for equipment, IoT-based energy management, and worker safety as top IoT trends in the manufacturing industry. In the image below, you can see how much investment these and some other IoT use cases are projected to get.
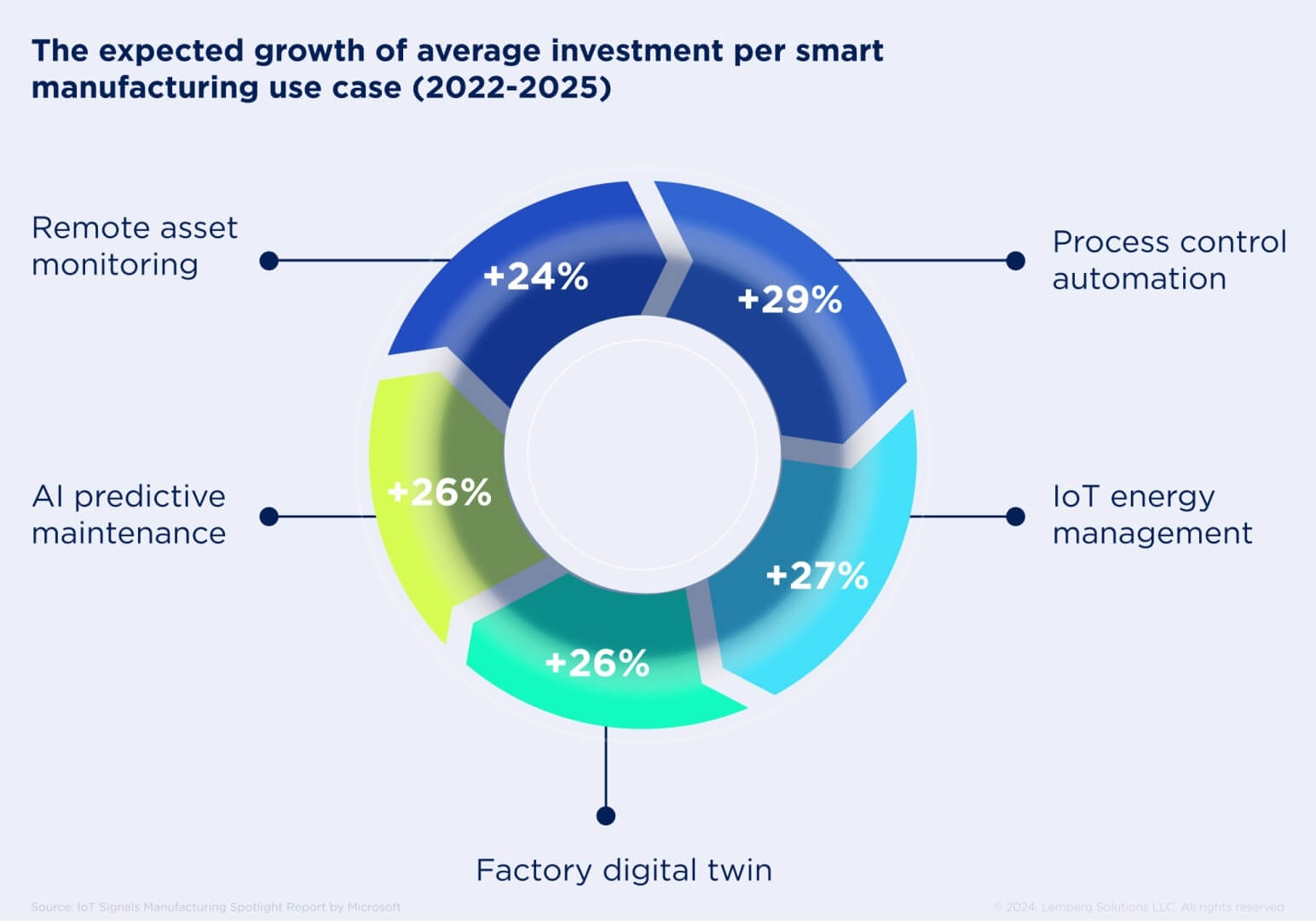
Further, we covered some more distributed IoT applications in manufacturing and outlined what benefits you will acquire with these use cases.
Remote device monitoring
Industrial IoT devices are integrated with sensors that capture particular data types in real time, analyze them, and display processed data on a web dashboard, mobile app, and other solutions available for end users.
This information lets you make critical decisions regarding regular machinery maintenance, planning repair, and production process metrics. Such a data-driven approach can also be used for global manufacturing and other vital business decisions.
Here you can learn more about the TCC electronic nurse device that ensures remote digital patient care, where we took on firmware and hardware engineering.
Read also: How to Manage an IoT Device Remotely: A Guide for Manufacturers and Enterprises
Digital twins
Digital twin is a software-based simulator of the manufacturing process that is one of the most significant IoT in manufacturing examples. Based on the data received from IoT sensors, the digital twin simulates production processes for testing before going live. Also, it allows engineers to perform experiments to discover hidden threats and potential issues without impacting or damaging the equipment itself.
Data analytics
IoT focuses on continuous data collection according to the set criteria, for instance, final product quality, machinery operation, energy consumption, and other metrics you require. Real-time data gathering and processing provide identification of machinery anomalies and complex patterns to predict issues and prevent them from evolving.
Asset tracking
Combining IoT and RFID technologies helps achieve automated and efficient asset tracking, which is pivotal for the speed of the manufacturing process and logistics.
Each unit's ID contains information about a serial number, model, assigned employee, location, purpose, and other parameters. If a particular asset is moved from one area to another, this information is scanned via tag and sent to the cloud database, where you access this information immediately.
It speeds up and optimizes asset tracking, eliminating the probability of human error and decreasing this load from your employees.
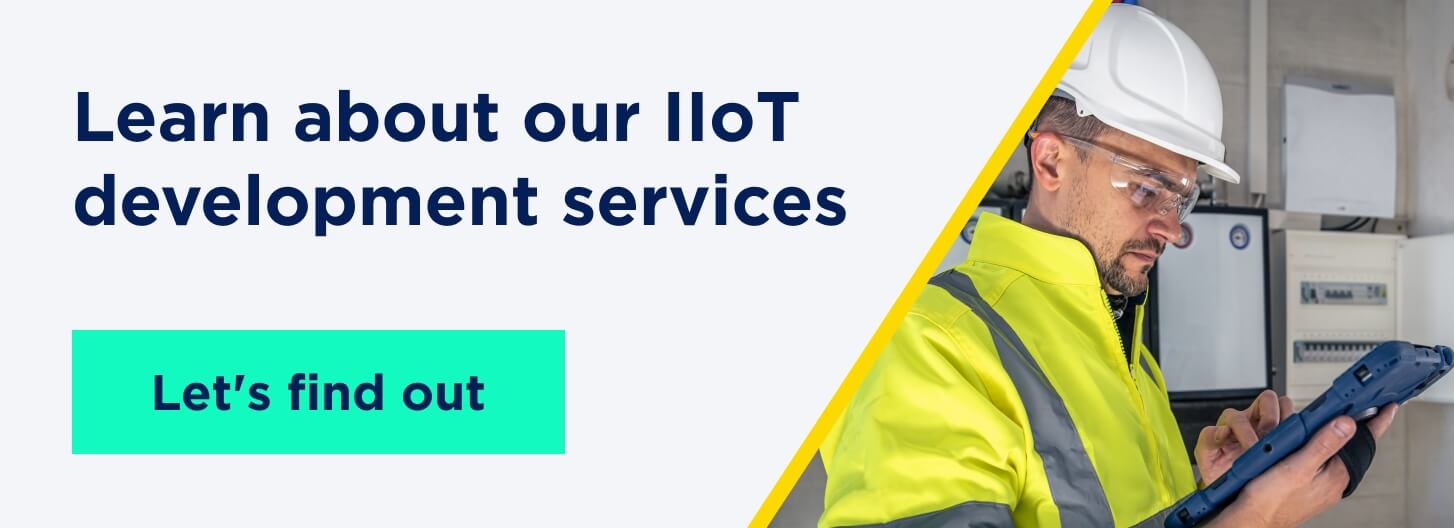
Benefits of IoT in manufacturing
Industrial IoT manufacturing devices help you achieve the maximum visibility of the production processes, providing real-time monitoring, detecting premature quality issues, and overall process optimization. Let's take a closer look at the business assets IIoT in manufacturing introduces.
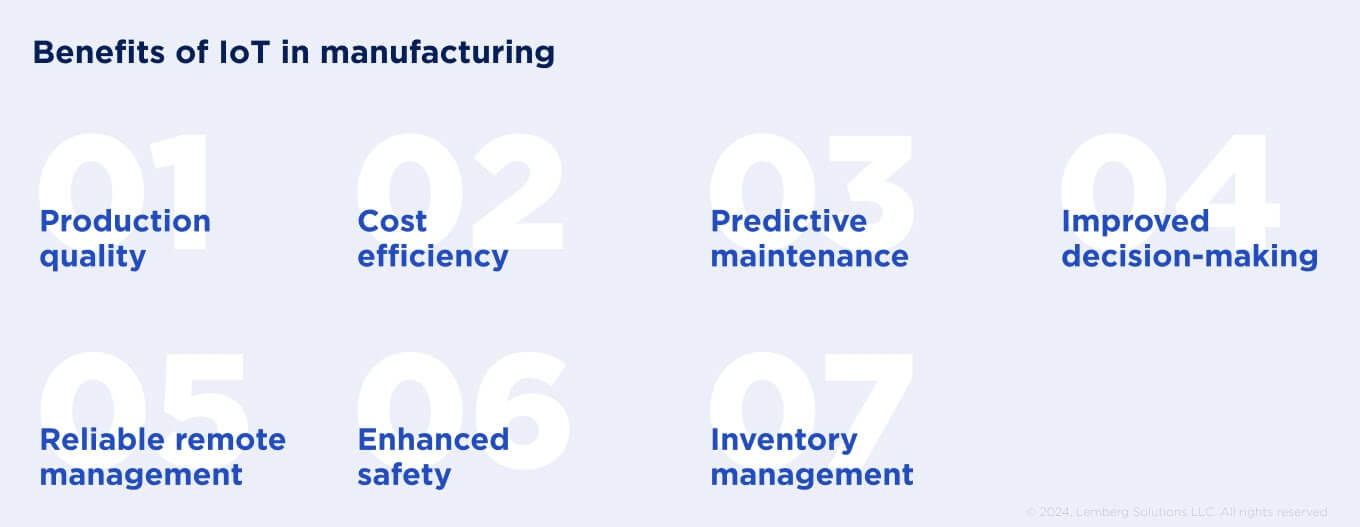
Production quality
Thanks to real-time manufacturing process monitoring, IoT-powered devices can alert about potential equipment malfunction or downtime in advance to prevent or fix these issues before they impact the quality of the final products.
Cost efficiency
IoT makes manufacturing equipment possible to manage remotely, including inspection, maintenance, and collecting data in environmental conditions. Due to the above-mentioned process, automation decreases manual work and staff, and the company's overall costs are reduced.
IoT sensors also assist in optimizing energy consumption due to the round-the-clock energy monitoring and usage analysis.
Predictive maintenance
Integrated sensors within machinery and other manufacturing equipment allow you to track environmental conditions, detect anomalies early, and provide on-time inspection and repair. This approach helps avoid durable equipment and production disruption or downtime, ensuring product quality and increased manufacturing productivity.
Improved decision-making
To ensure data-driven business decisions, it is vital to understand what type of data you need to collect and how to collect it properly to get valuable insights. With the integration of a data analytics system, you can analyze historical data to forecast manufacturing failures, preventing equipment malfunction and decreasing downtime.
Reliable remote management
IoT advances the visibility and management of manufacturing remotely, resulting in a more efficient product development life cycle. You can partially predict the potential issues and machinery downtime, measure the final product quality, and oversee all production iterations to deliver the marketable product much quicker.
Enhanced safety
Despite the production volumes, safety remains a top priority for business owners in two directions — machinery and staff. Integrated IoT sensors allow you to expose risks for your employees by detecting potential machinery crashes, recognizing humans to avoid harm, and alerting them about equipment damage.
To establish machinery safety, you can classify and set equipment safety parameters and enable alerts and system shutdown in emergencies.
Inventory management
Inventory management is of paramount importance for manufacturing companies of any scale. The Internet of Things in manufacturing provides the capability to manage assets at all production processes and levels. You get updated about the stocks and equipment at warehouses in real time. It helps avoid overstocking and understocking, ensuring their availability and integrity.
How IoT is transforming the manufacturing industry: top 6 trends 2024
Manufacturing digitalization, or Industry 4.0, is indispensable for companies that aim to keep their business thriving, growing, and competitive. In 2024, we will see new areas of IoT advancements in the industry and how these tech trends will affect the production processes and delivered product quality.
Let's examine upcoming IoT applications to watch in the following year.
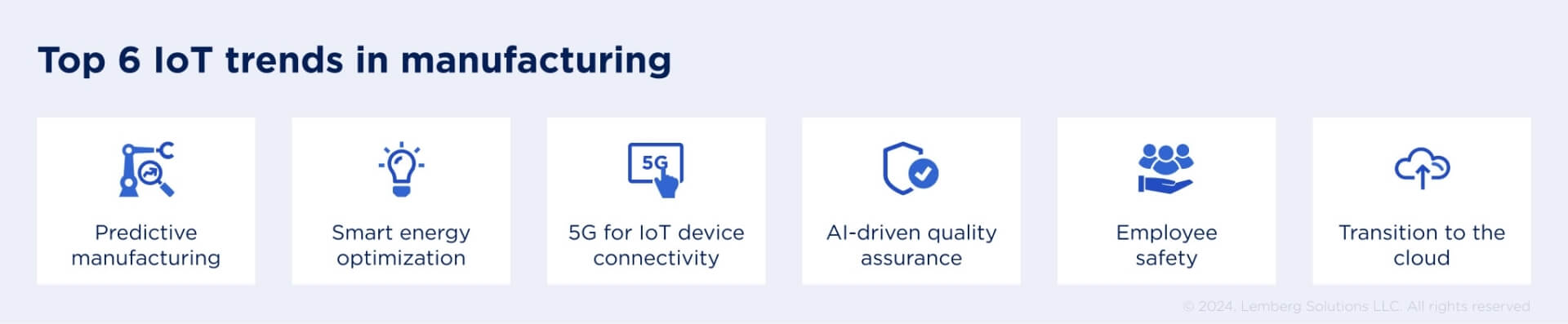
1. Predictive manufacturing
Predictive manufacturing is an approach to predictive analytics and maintenance of IIoT devices that will keep evolving in 2024. To get and maintain a competitive edge in the industry, manufacturing companies should consider decreasing maintenance costs and avoiding durable machinery downtime, ensuring an unceasing and quality production process.
Predictive manufacturing analytics collect real-time data from IoT devices and use historical data collected previously from the same sensors to analyze it and provide insights. It allows you to define patterns in your production processes and make data-driven decisions with predicted outcomes regarding the products' quality, demand, efficiency, and overall cost.
2. Smart energy optimization
Energy monitoring is one of the critical indicators to track and measure in manufacturing constantly. It allows you to track the energy consumption within your production processes and find the inefficient energy usage that impacts the costs and quality of equipment predictive maintenance. Also, energy management will help you align its usage with industry energy regulations and your business goals.
3. 5G for manufacturing IoT device connectivity
Implementation of 5G is a rising tech trend in manufacturing that is projected to keep growing in 2024 and supporting industry technical advancements like IoT, AI, AR, and others. According to recent statistics, in the following year, 5G has the potential to evolve 2.1 times compared to 2023.
Compared to 4G and Wi-Fi IoT device connection, 5G will introduce low latency and continuous data collection from IoT-enabled devices, the capacity to interconnect a giant number of devices, ensuring their stable communication. Additionally, it leads to lower costs, which is crucial for large manufacturing companies.
However, this tech trend is currently at the outset of a comprehensive implementation in manufacturing. Nonetheless, we'll see significant benefits and achievements of 5G connectivity for predictive maintenance, manufacturing-as-a-service, precision device monitoring, and other use cases in the next 2-3 years.
4. AI-driven quality assurance
Powered with artificial intelligence, industrial IoT devices ensure product quality and make timely and remote adjustments. Integration of AI within IoT devices allows the visual inspection of production processes via real-time video and/or audio monitoring. Thus, you can detect anomalies or equipment faults and make critical decisions to avoid releasing low-quality products.
5. Employee safety
To establish an uninterrupted and smooth manufacturing process, employee safety must be one of the top priorities in your plan. Approximately 1740 workplace injuries were reported in manufacturing during the last year.
IoT is already broadly used for managing staff and their safety in several ways. The first one is the integration of detection sensors into the manufacturing equipment that recognize humans and stop functioning until the human is not in a safe place.
Another IoT application to ensure employee safety is wearables that help technicians track their health conditions and prevent critical situations.
Nonetheless, the potential of IoT for safety is not limited by the two examples above, as integrated sensors can also measure equipment temperature to prevent fire and detect gas leakage.
6. Transition to the cloud
More manufacturing companies are willing to migrate their on-premise digital system to the cloud, and we explain why. IoT sensors collect and transmit vast volumes of data to the on-premise database on a daily basis. That's why more manufacturers migrate their software to the cloud, ensuring secure and structured data storage with restricted access.
Cloud-based manufacturing systems are scalable to collect and save as much information as required, consume less energy, and are cost-efficient in maintenance. Migration to the cloud also enables internal collaboration, allowing employees to access the required data wherever they are and whatever they need according to their permission.
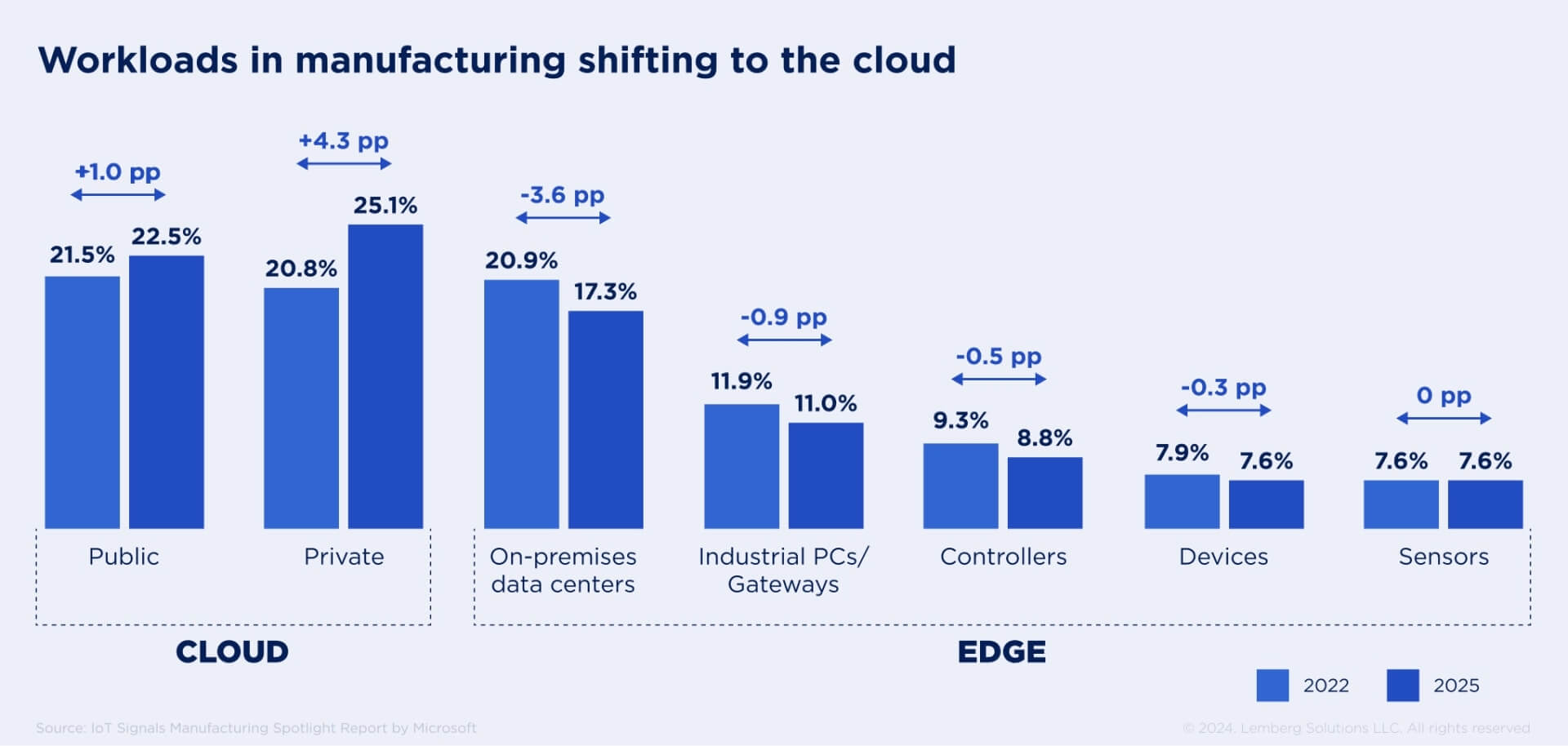
Challenges of IIoT Adoption
Along with beneficial options, Industrial IoT implementation leads to various considerations each manufacturing business may face. It concerns the complexity of IoT system implementation, maintenance costs, data processing, and storage. So, let's look into the key challenges to expect.
Legacy manufacturing equipment
Legacy equipment may become one of the primary challenges in IoT adoption as it is not integrated with IoT-based connectivity.
As a practical solution, refactoring obsolete manufacturing facilities unlocks the IoT advantage for the entire production process. This process includes integrating sensors, communication protocols, and other components to ensure real-time data collection and round-the-clock connectivity of devices with software.
IIoT device security
Industrial devices connected with IoT are exposed to a wide range of security threats, which results in risks of data loss, data leak, and manufacturing process disruption.
That's why vital IoT devices comply with data security and industry standards and implement a cybersecurity strategy that includes data encryption, data backups, and access control policy.
IoT expertise gap
You may face two main struggles with IoT adoption: lacking the knowledge to start IoT transformation or lacking an exact solution to fit your needs.
The most effective way to resolve ongoing issues is professional tech consulting from IoT experts like Lemberg Solutions. We`ll develop IoT sensors, dashboards, cloud and AI-based software systems, or other IoT solutions for the manufacturing industry your business needs. Also, have a look at the skill gap mitigation strategies companies consider as efficient.
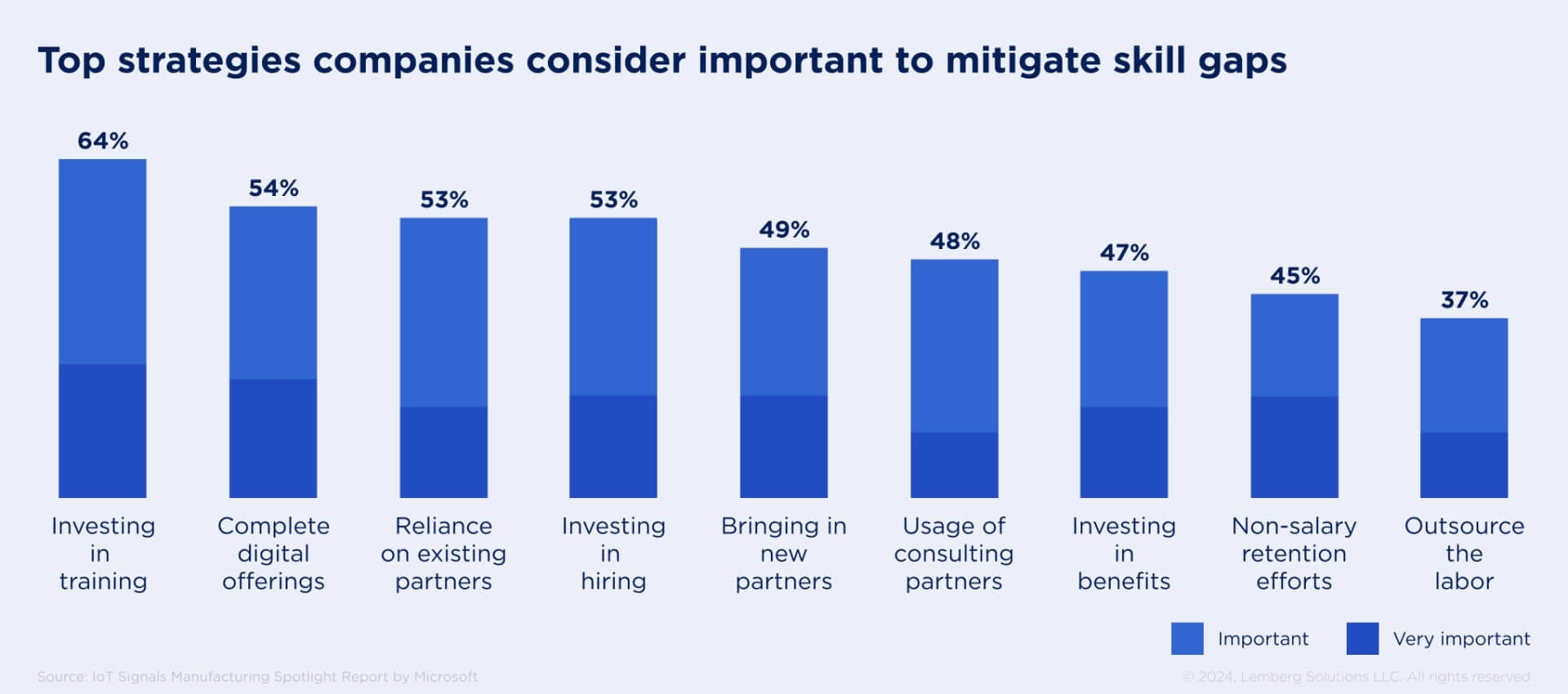
Final thoughts
IoT implementation opens up substantial opportunities for manufacturing companies, ensuring expected uptime and optimizing resources and costs, thereby boosting overall production productivity.
Building a precise IoT implementation strategy based on your business specifics, issues, and current requirements is pivotal to ensure that IoT adoption flows successfully within your organization.
Enable IoT potential for your production by leveraging our IoT development services expertise. We'll help you review your ongoing solutions to find an improvement plan or assist you with building the entire infrastructure for your custom IoT solution.
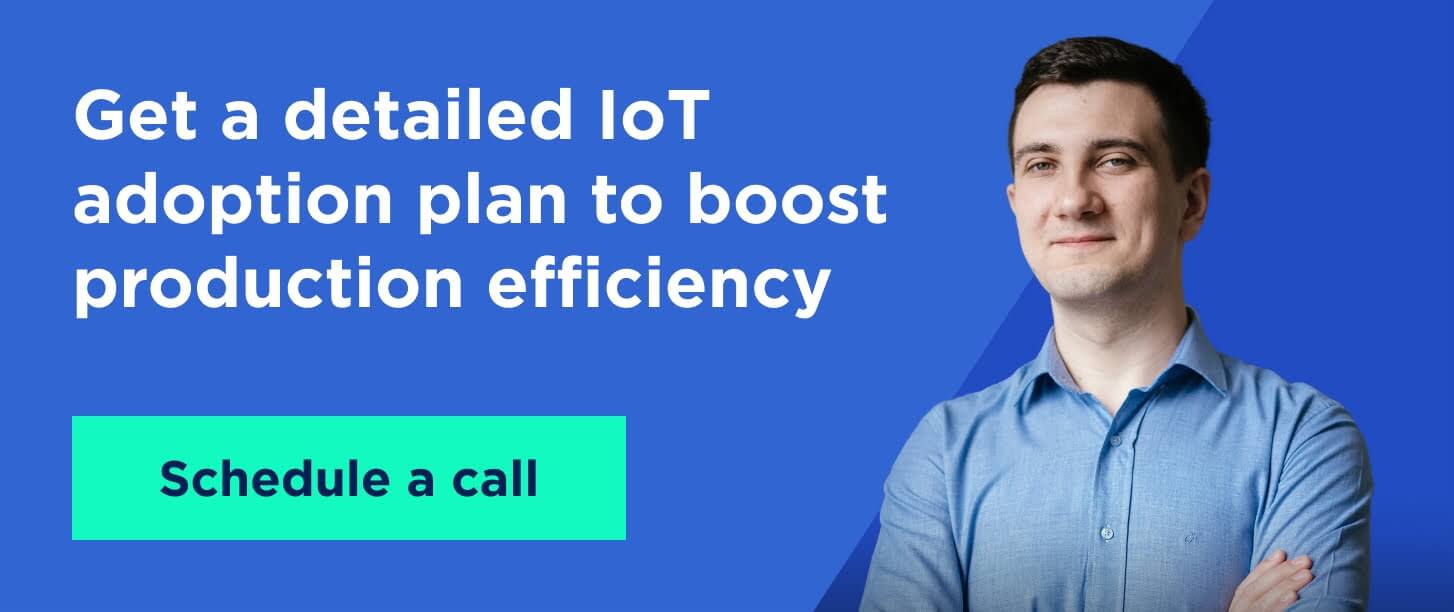
FAQ
What is IoT, and how is IoT used in the manufacturing industry?
IoT helps create a single ecosystem with interconnected devices integrated with sensors accountable for specific functions within each device. The use of IoT in the industry helps boost overall production efficiency, reduce costs, and prevent downtime by interconnecting all machinery units into one working system.
Why is IoT important in manufacturing?
IoT is an indispensable technology for manufacturing companies to make data-driven business decisions and adequately manage production processes. Constant process monitoring and improvement lead to quality products, equipment predictive maintenance, optimized energy usage, and a safe working environment.
Why is IoT adoption gaining momentum in the manufacturing sector?
Despite the current application, IoT has massive potential in manufacturing, allowing you to collect and analyze data from the production process in real time. It helps you properly allocate internal resources, make informed decisions, and make all processes transparent and more productive.