Creating and implementing a suitable hardware design defines the operability and efficiency of the entire product. Today, the range of integrated circuits and their design processes has considerably expanded, complicating the choice for product engineering and manufacturing.
This article compares two different hardware design approaches that entail using FPGA or ASIC integrated circuits. It outlines which solution is more cost-efficient, the duration of development and manufacturing, flexibility, and overall embedded system performance.
This material will help you clarify the differentiators of the FGPA and ASIC design flows. We will emphasize the importance of choosing integrated circuits in the entire embedded product development process to simplify this step for your project.
What Is an ASIC?
ASIC stands for Application Specific Integrated Circuit integrated on a chip to perform a specific function. This type of integrated circuit cannot be reconfigured, which means it can only function for its initial purpose.
Types of ASICs
There are three different types of ASIC, such as:
- standard cell ASIC - consists of library components or functional blocks you can customize to perform specific functions within the product;
- gate array ASIC - comprised of silicon layers you can adjust only via transistor interconnection in the manufacturing stage;
- fully custom design ASIC - transistors and their logic can be designed per specific request.
ASIC design process
Compared to FPGA, ASIC design flow is more complicated and time-consuming. It includes chip design specification, architecture, functional modeling, synthesis, placing and routing, testing, and implementation. This process applies to each integrated circuit that performs a particular function within an embedded system.

Advantages & disadvantages of ASICs
The advantages and disadvantages are relative, as whether this IC suits your project depends on product specifications. Check the benefits and pitfalls related to ASICs to understand the potential of this technology on your project.
Pros:
- Available for mass production
ASICs are suitable for large-volume production. Even though NRE costs are higher than FPGAs, this IC type becomes a cost-efficient solution in the long run, ensuring custom-made functionality.
- Lower power consumption
ASIC consumes less power as compared to FPGA, as it doesn't have extra transistors and logic, which commonly require additional power if the conditions are stable.
- Ultimate customization
ASICs offer a high level of customization, allowing designers to create chips tailored to the exact requirements of their application. This results in improved efficiency and better alignment with the system's needs.
Cons:
- No design upgrades are possible
Once the ASIC design is created and released, it cannot be modified. If you need to improve the design, change logic, or enhance the algorithm, embedded engineers must set up another ASIC layer in the system or redesign and remake the entire product from scratch.
- Durable prototyping
Creation ASIC in the silicon is a durable and very costly process. In addition, it requires thorough attention as ASICs are not reprogrammable, so it is pivotal to ensure each function will work correctly.
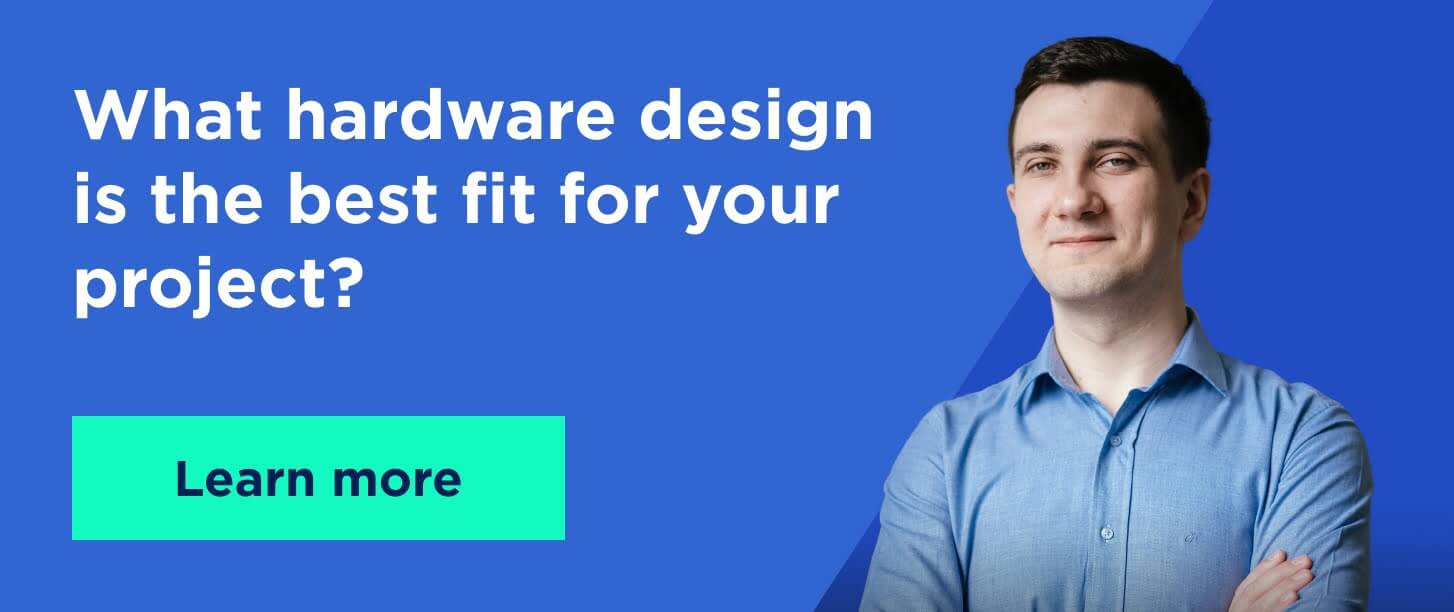
What Is an FPGA?
FPGA is a field programmable gate array comprising numerous configurable interconnected logic blocks. You can design and program this integrated circuit to perform the expected function like a graphics card or reprogram it so that the same circuit performs another action like a microprocessor. Such capabilities allow changing the existing product functionality by updating software without any manufacturing and physical design change.
FPGA design process
The FPGA design process consists of three main steps - entry, synthesis, and implementation. The entry stage includes designing logic blocks and their correct interconnections. Synthesis entails real-time input and output data processing within the logic blocks, while implementation is about logic block deployment and routing.

The FPGA design process takes way less time than ASIC`s, so this would be a good fit for products you need to produce and launch to market quickly. However, FPGAs are much more costly, so if plan to launch a mass production, ASICs are a more cost-efficient solution.
Read also: FPGA Programming: When to Use FPGAs in Your Embedded System
Advantages and disadvantages of FPGAs
Outlining some of FPGAs' benefits and minuses will help you clarify which technology would be a better fit for your project requirements. You can also contact our embedded experts and schedule a call to consult on the integrated circuit to implement.
Pros:
- Reprogrammability
Reprogrammable elements have many practical benefits for two reasons: you can change the function purpose without re-engineering the chip after its installation or fix the system errors more simply by reconfiguring the element setup.
- Single-chip solution
Using a single FPGA chip gives the ability to implement an embedded system with all required features to receive the expected system performance. Also, the FPGA configuration can be adjusted and changed to provide new features for your system.
- Lower NRE
Again, thanks to the reprogrammable nature of FPGA, it requires lower non-recurring engineering (NRE) costs as you don't have to integrate new integrated circuits to obtain the required functionality.
Cons:
- Additional integrated circuits
You won’t be able to configure certain features in your embedded system with an FPGA, so engineers must add more integrated circuits to implement the expected system functionality. It causes higher NRE cost, but as FPGAs are unsuitable for mass production, using this IC will keep the budget on track, just like using an ASIC chip.
- Not suitable for mass production
FPGAs are not a cost-efficient solution for mass production. This IC is an excellent choice for prototyping, but for further high-volume manufacturing, ASICs are more cost-efficient.
- More durable launch
FPGA configuration is stored in the external flash. So, FPGA needs more time to load the chip to make it operate than ASIC. This factor can be decisive in certain types of circuits.
The main difference between ASIC and FPGA
Let's summarize the key differentiators of ASIC chip vs FPGA. However, the choice still depends on the type of product you want to create, its functions, budget, production volume, and how fast you want to launch to the market. Also, you can set up a consultation with our embedded development services team to define your product core requirements and decide on the material to use.
Option | ASIC | FPGA |
---|---|---|
Flexibility | ASIC is designed and integrated to perform a certain fixed function with no ability to reprogram it | FPGA is a reconfigurable chip where interconnected logic blocks can have a custom purpose |
Performance | Performs better as each function is already set | Reprogrammable nature causes lower performance |
Power consumption | Consumes less power due to the functionality-specific design | Consumes more power performing the same functions as ASICs |
Time to market | More suitable for long-term projects as the design process has 8 steps and takes a lot of time | Fast time to market due to the quicker design process with 3 main stages |
NRE | ASICs provide higher NRE cost, but thanks to functionality layering, it can also be changed or expanded on-premise | FPGAs provide lower NRE as this integrated circuit is comprised of thousands of logic blocks that can be reconfigured |
Design flow | Consists of eight main steps, which result in a more time-consuming design process | Consists of three main stages only ensuring fast time to market |
ASIC vs FPGA: which one should you choose?
Considering the similarities and differences between FPGAs and ASICs, there is no correct answer as to which one you should choose for developing a product. It ultimately depends on your core product requirements and project timeline, budget, and manufacturing expectations. Below, we cover the widespread cases of using ASICs and FPGAs.
FPGA is the best choice for developing an embedded system that will be easy to scale with thousands of additional units, allow reprogramming certain functions to perform other tasks, and consume less energy. For example, you can use FPGAs for medical devices, automotive embedded systems, energy management solutions, etc.
ASIC also provides low power consumption, which makes it suitable for energy-sensitive solutions. It also ensures lower unit costs and makes the product more suitable for mass production.
FPGA vs ASIC comparison summary
As you can see when comparing FPGA and ASIC, these hardware design approaches have multiple applications as well as pros and cons. The choice of the right approach depends on your project specifications, business requirements, and capabilities. The core characteristics you need to take into account are product complexity, expected production volume, available budget, prototype necessity, and market launch deadlines.
You don't have to decide on the hardware design approach on your own, as our skilled embedded engineers are ready to consult you on any question. We will help you outline the project's core requirements and proceed with the product design, development, testing, and launch.
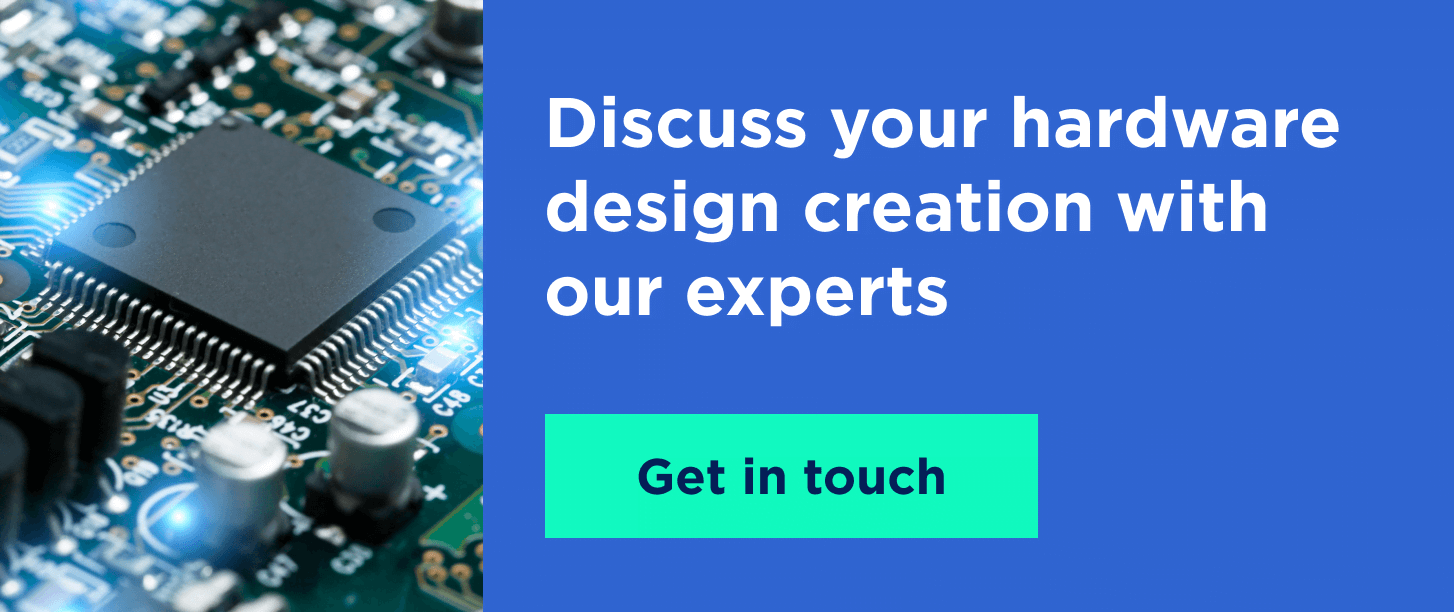